Understanding a welded wire gauge chart is essential for anyone involved in construction, manufacturing, or fencing projects. These charts provide crucial details that determine the strength, durability, and flexibility of the wire mesh, which are vital for ensuring structural integrity and safety in various applications. This article delves into the nuances of welded wire gauge charts, providing insights that underscore expertise, credibility, and reliability.
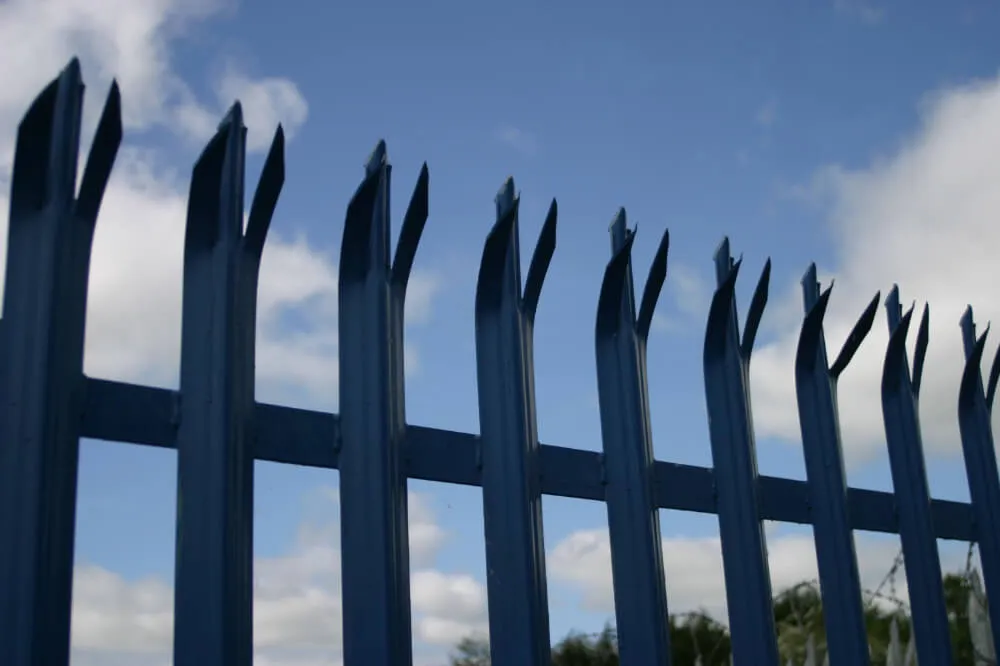
Welded wire gauge charts present information on wire diameters, mesh openings, and other key attributes in different gauges. The gauge of wire indicates its diameter, with smaller numbers representing thicker wire. For example,
wire gauge 10 is thicker than wire gauge 14. This system may seem counterintuitive at first, but it harks back to historical manufacturing processes that defined the gauge based on the number of operations required to produce the wire.
When consulting a welded wire gauge chart, it's imperative to understand the direct correlation between wire gauge and performance characteristics. Thicker gauges (lower numbers) typically offer enhanced strength and durability but can be less flexible and more challenging to manipulate. Conversely, thinner gauges (higher numbers) are easier to work with but may not provide the same level of strength and durability. Selecting the appropriate gauge is crucial and hinges upon the intended application.
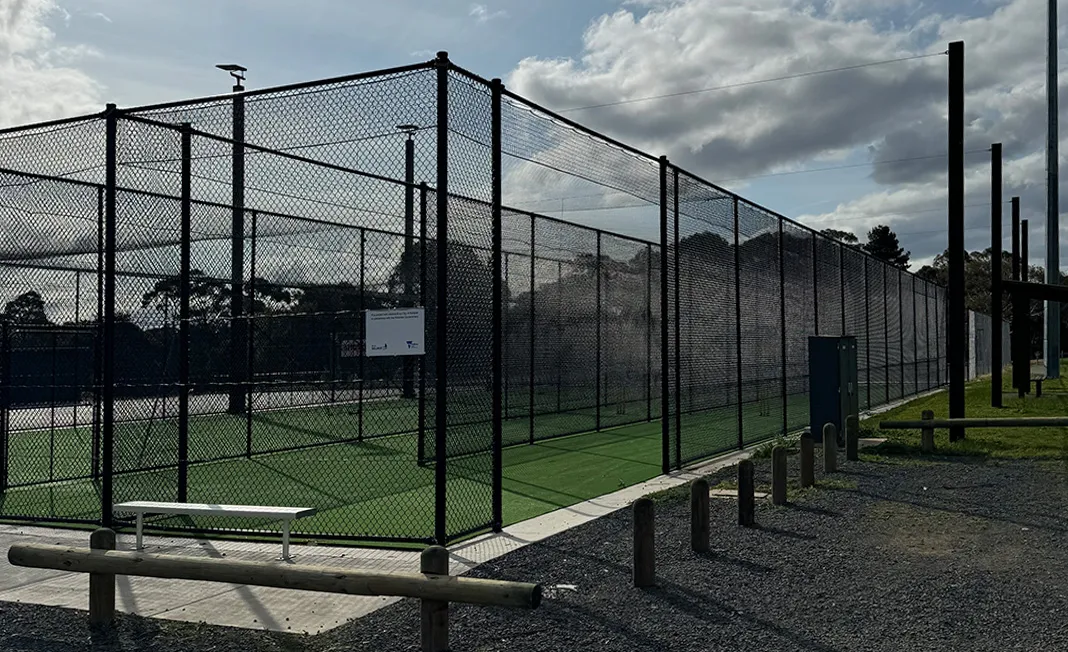
For instance, in constructing a reinforced concrete slab, heavier wire gauges might be preferred to provide the necessary support to withstand the considerable weight and physical stress. Meanwhile, for projects like garden fencing or lightweight enclosures, a lighter gauge can suffice, offering cost-efficiency and ease of installation without compromising functionality.
Authoritative sources, such as industry-standard organizations, specify guidelines recommending ideal gauge sizes for different applications. Consulting these resources ensures adherence to safety and quality standards. Furthermore, collaborating with suppliers who have demonstrated expertise in the field can offer valuable guidance. These suppliers typically have years of experience and can provide customized solutions tailored to specific project requirements, reinforcing credibility in your selections.
welded wire gauge chart
The material composition of the wire also plays a vital role. Whether opting for galvanized steel, stainless steel, or another metal, each option has distinct properties influencing corrosion resistance, tensile strength, and lifespan. For instance, galvanized wire is prized for its corrosion resistance, making it ideal for outdoor applications where exposure to the elements is a concern. On the other hand, stainless steel offers superior strength and is often favored in industrial applications requiring high resilience to physical and environmental stressors.
Trustworthiness is established through rigorous testing and documentation. Reputable manufacturers often provide certifications and test results demonstrating the wire's compliance with recognized safety and quality standards. These certifications are a testament to the reliability and performance of the wire mesh, giving consumers confidence in their purchase decisions.
Moreover, exploring real-world experiences from professionals who have employed different gauges in various scenarios can significantly enhance understanding. Expert testimonials often reveal insights that technical charts alone cannot convey, such as the ease of handling during installation, long-term performance under specific conditions, and any unforeseen challenges encountered during application.
When selecting welded wire mesh, it is beneficial to conduct a comparative analysis of different gauges in relation to cost, ease of installation, anticipated environmental conditions, and expected load-bearing requirements. Such comprehensive scrutiny ensures a well-informed choice that aligns with project goals and budgetary constraints.
In summary, mastering the intricacies of welded wire gauge charts is a blend of technical knowledge and practical experience. By prioritizing established industry standards, leveraging expertise from seasoned professionals, and verifying through direct, certified information, individuals and businesses can make informed decisions that enhance project outcomes. The selection process, driven by a balance of professional advice and authoritative guidance, leads to trustworthy and efficient solutions tailored to specific needs. As the construction and manufacturing industries evolve, so too does the need for ongoing education and adaptation, ensuring continued excellence and safety in all applications involving welded wire mesh.