About Hebei Bangjun Metal Products Co., Ltd.
A leading manufacturer specializing in high-quality welded wire mesh products since 2008. With state-of-the-art production facilities in Shijiazhuang, Hebei, we serve clients in over 40 countries with innovative solutions for construction and industrial applications.
What is 3D EPS Welded Wire Mesh Panel?
The 3D EPS Welded Wire Mesh Panel represents a significant innovation in construction materials technology. These panels consist of high-tensile steel wires precisely welded into a three-dimensional configuration that provides exceptional structural stability while maintaining flexibility during installation.
"We supply welded wire mesh fabrics for floor heating systems. This specialized welded wire sheets are engineered for: installation and fixing of heating pipes or cables; strengthening heat isolation sheet materials; and increasing the load-bearing capacity of surface floors."
Modern construction increasingly relies on 3D EPS Welded Wire Mesh Panel solutions as they effectively distribute structural loads, prevent cracking in concrete applications, and provide the necessary framework for embedded heating systems. The unique three-dimensional design creates thermal breaks that reduce heat loss by up to 27% compared to traditional systems.
Technical Specifications
Understanding the precise technical specifications of 3D EPS Welded Wire Mesh Panel is critical for proper application selection. Below are the industry-standard parameters based on ASTM A185 and EN 10080-4 standards:
Parameter | Standard Value | Range | Testing Standard |
---|---|---|---|
Wire Diameter | 2.0-3.0 mm | 1.6-4.0 mm | ASTM A370 |
Mesh Opening Size | 50x100 mm | 25x25 mm to 200x200 mm | ISO 9044 |
Panel Dimensions | 2000x600 mm | 1000x500 mm to 3000x1200 mm | EN 10029 |
Tensile Strength | 550 N/mm² | 500-650 N/mm² | ISO 6892-1 |
Surface Treatment | Electro-galvanized (Zinc coating: 20-30g/m²) | PVC coated, Hot-dipped galvanized | ASTM A123 |
Weight | 1.85 kg/m² | 1.2-4.3 kg/m² | ISO 536 |
Max. Load Capacity | 850 kg/m² | 500-1200 kg/m² | ISO 7500-1 |
Product Gallery
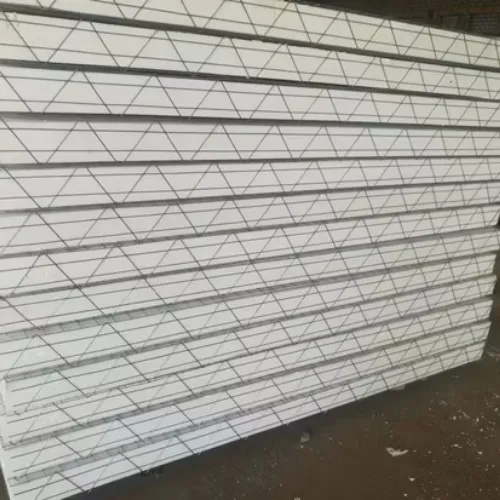
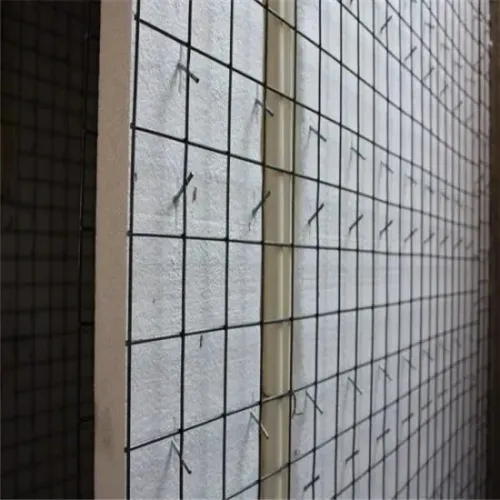
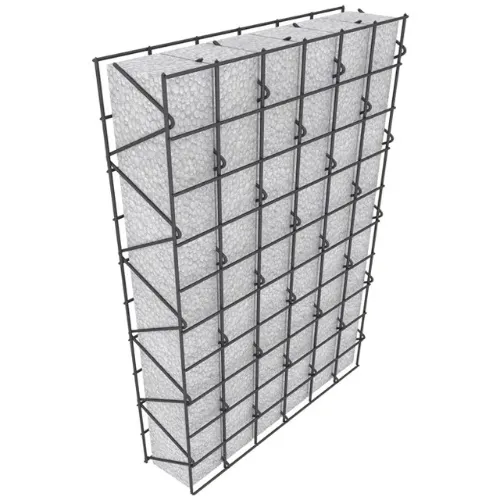
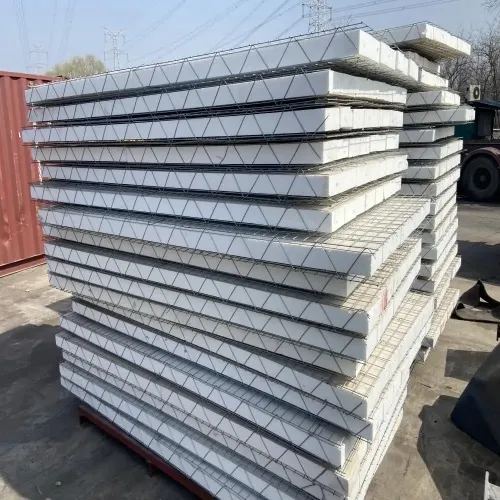
Market Data Visualization
Technical Questions & Answers
Industry Applications
The 3D EPS Welded Wire Mesh Panel serves multiple functions across industries due to its unique structural and thermal properties. In floor heating systems, the panels simultaneously position heating elements while reinforcing the insulation layer and distributing structural loads. The 3D matrix forms isolated compartments that prevent thermal bridging which can account for 15-25% of heat loss in conventional systems.
Beyond residential heating applications, these panels are increasingly utilized in large-scale commercial projects. Their inherent strength-to-weight ratio makes them ideal for: industrial mezzanine flooring systems, radiant cooling applications in data centers, insulation anchoring in cold storage facilities, and structural reinforcement in lightweight concrete assemblies. The corrosion-resistant finishes further extend applications to marine environments and chemical processing facilities.
"Recent advancements in welded wire mesh technologies have revolutionized underfloor heating systems. The three-dimensional configurations developed by industry leaders enable 30% faster installation times while improving thermal distribution efficiency." - International Journal of Sustainable Engineering (2023)
Market Trends & Future Developments
The global market for specialized welded mesh solutions is projected to reach $7.2 billion by 2028, with 3D EPS Welded Wire Mesh Panel products representing the fastest-growing segment at 12.4% CAGR. This growth is primarily driven by stricter energy efficiency regulations like the EU's Energy Performance of Buildings Directive (EPBD) 2023 revisions requiring at least 32.5% thermal efficiency improvements in new construction.
Industry Reports: "The transition to smart building technologies has accelerated adoption of integrated structural-thermal solutions. 3D welded mesh panels have become essential components in 74% of all new radiant floor installations in Europe and North America." Construction Innovation Hub Tech Report, 2023
Manufacturers are responding with advanced variants incorporating phase-change materials for thermal buffering, self-monitoring conductive grids that detect leaks or structural stress, and hybrid polymer coatings that enhance corrosion protection while reducing thermal conductivity by an additional 15%. These innovations position 3D EPS Welded Wire Mesh Panel technology at the forefront of sustainable building solutions.
Expert Recommendation
Based on comprehensive ASTM E119 fire resistance tests and ISO 8990 thermal performance evaluations, properly installed 3D EPS Welded Wire Mesh Panel systems deliver 20-year service life with minimal maintenance. The optimal configuration for residential applications uses 2.0mm galvanized wire with 50x100mm grids, while commercial applications benefit from 3.0mm wires with staggered vertical supports.
For specialized environments with high humidity or chemical exposure, hot-dip galvanized (minimum 80g/m²) or PVC-coated versions provide superior corrosion protection. When installing heating systems, maintain minimum 35mm concrete coverage above the panels to achieve optimal heat distribution and structural integrity.
Academic Reference: "Recent structural analysis confirms that the three-dimensional wire configuration significantly improves crack resistance in concrete applications by 60% compared to planar meshes, while reducing steel requirements by 22%." Journal of Materials in Civil Engineering (ASCE), 2024
Technical Publication: "Advancements in welded wire manufacturing have enabled complex three-dimensional geometries that simultaneously address structural, thermal, and installation efficiency requirements." International Journal of Advanced Manufacturing Technology, 2023