Ensuring the stability and longevity of any architectural or engineering project often hinges on the reliability of its components. In the context of render mesh fixings, these unassuming elements play a pivotal role in the structural integrity and aesthetic value of building facades. As construction professionals increasingly rely on render meshes to prevent cracking and ensure smooth finishes, understanding the nuances of render mesh fixings becomes paramount.
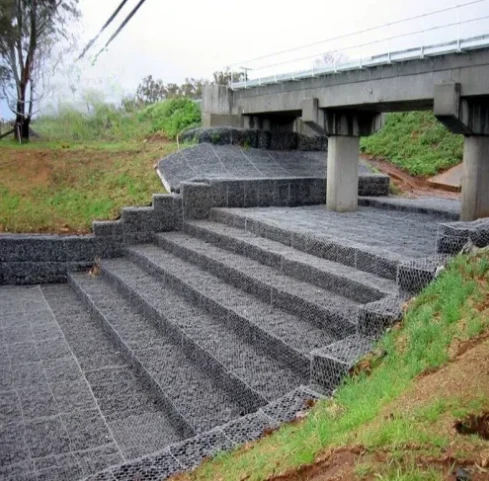
When delving into the world of render mesh fixings, one begins to appreciate the blend of engineering artistry and practical application. The choice of the right fixing is not merely about selecting a component that meets basic requirements; it involves an informed decision based on material compatibility, environmental conditions, and anticipated mechanical stresses.
Expertise in this domain reveals that the selection process for mesh fixings starts with understanding the composition of the render material. For lime-based renders, which are renowned for their breathability and flexibility, stainless steel or similarly non-corrosive fixings are advisable. These fixings resist rust and degradation, thereby prolonging the lifespan of the mesh and the render associated with it.
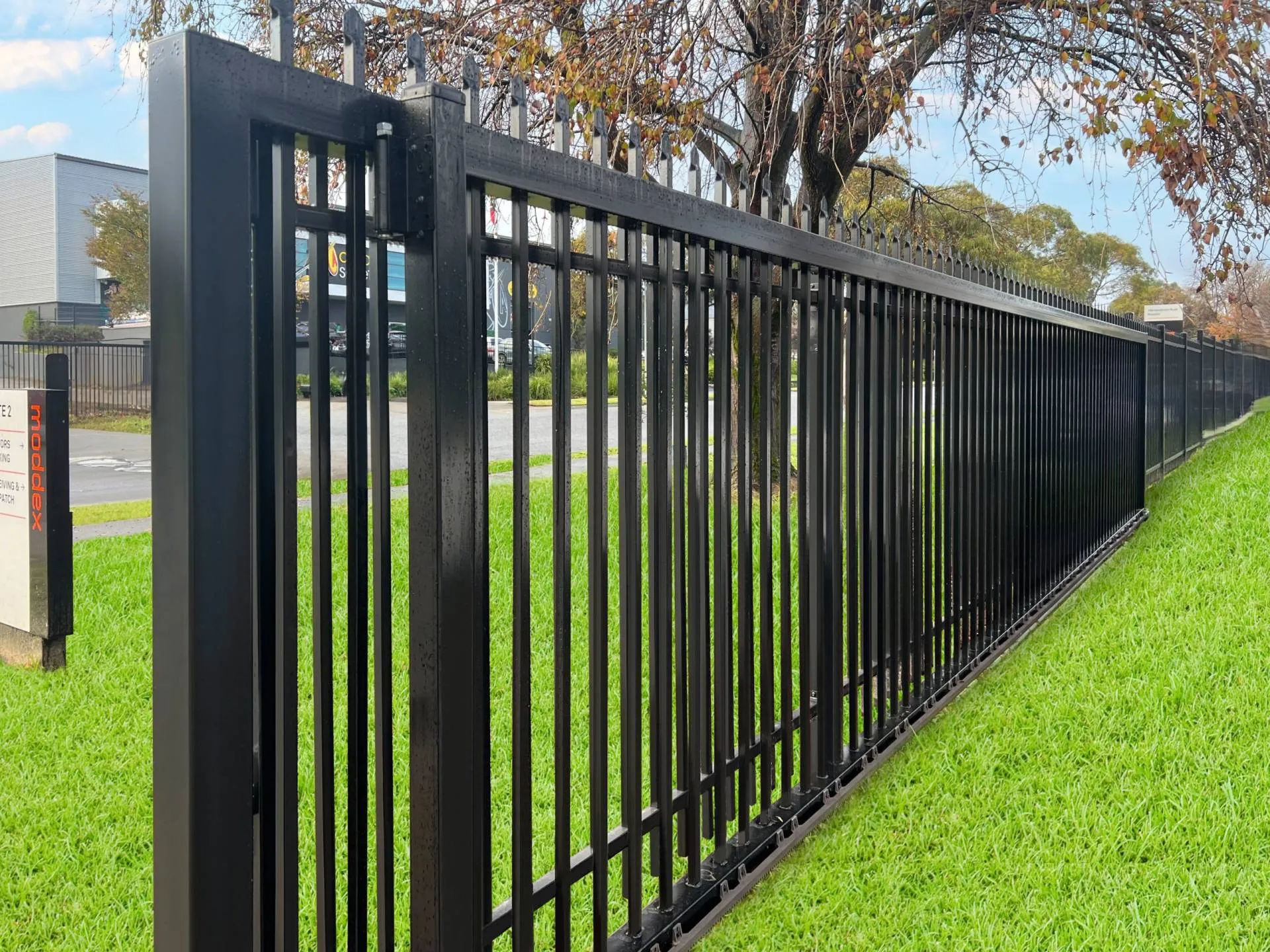
In scenarios involving external insulation finishing systems (EIFS), the choice of fixings needs to accommodate the thermal expansion and contraction of the layers involved. Here, fixings with a high degree of elasticity are beneficial, as they help in maintaining the structural bond between the render and insulation materials under varying temperature conditions. This choice not only enhances the integrity of the facade but also contributes to energy efficiency by reducing thermal bridging.
render mesh fixings
The impact of weather cannot be understated when discussing render mesh fixings. Projects situated in coastal areas, where humidity and salt content are considerably higher, demand fixings with exceptional anti-corrosive properties. Titanium and advanced alloy metals are becoming increasingly popular in such environments, offering longevity and resistance unmatched by conventional materials.
Providing a practical example, consider a recent project where render mesh fixings were meticulously chosen for a historic renovation. The building, exposed to wide-ranging temperatures and urban pollution, required fixings that could support a heavy, traditional lime render while coping with dynamic environmental conditions. By selecting a specialized fixing system, the renovation achieved not only aesthetic harmony with its historical context but also ensured the structural integrity of the facade for decades.
The authority of render mesh fixing expertise and product selection becomes a foundation for trustworthiness in client relationships. Professionals who integrate these high-caliber components demonstrate a commitment to durability and performance, often saving on future repair and maintenance costs consequently. As the industry evolves, continuous innovation from leading construction material manufacturers introduces new materials and systems that address past limitations, setting new benchmarks for quality.
Therefore, trusting in expertise when it comes to render mesh fixings is not merely an operational decision but a commitment to excellence in construction. Emphasizing the value of robust fixings positions a construction project not just for immediate success but for a legacy of quality, reinforcing trust and satisfaction in clients and stakeholders alike.