For those in the construction and reinforcement industry, welded wire fabric (WWF) stands as a foundational element that ensures the structural integrity and longevity of concrete infrastructures. Welded wire fabric, often utilized for reinforcing concrete slabs, pavements, and structures, is systematically manufactured using a series of parallel longitudinal wires, each welded to a set of perpendicular crossing wires.
This design not only optimizes reinforcement but also simplifies the concrete pouring process.
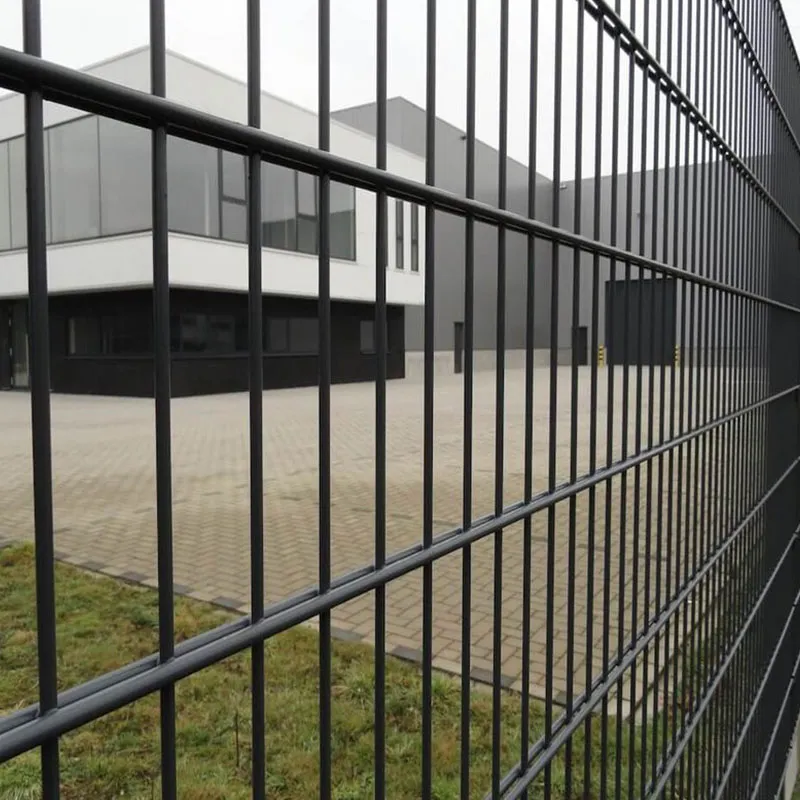
The experience of using welded wire fabric in various construction projects has shown its unparalleled versatility and efficiency. Unlike traditional rebar, which requires labor-intensive placement and tying on-site, welded wire fabric comes pre-assembled and ready for immediate installation. This time-saving feature is particularly evident in large infrastructural projects, where minimization of labor hours translates to substantial cost savings.
From the perspective of expertise, it is crucial to highlight that the application of welded wire fabric extends beyond mere cost-effectiveness. The precision in the spacing and alignment of the wires enhances the tensile strength of concrete, preventing cracks and structural failures even under heavy loads. This quality stems from the fact that precast welded wire panels maintain consistency in design and structural properties that individual onsite rebar configurations may lack. Industry experts advocate for the use of WWF in conditions where environmental exposure and load unpredictability are concerns, ensuring that the reinforced concrete maintains its integrity under varied stress conditions.
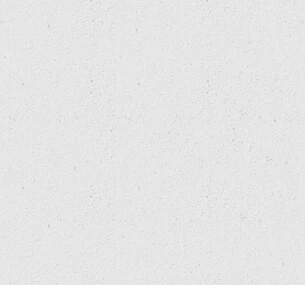
welded wire fabric
Positioning welded wire fabric as a product infused with authoritativeness lies in its alignment with international standards and certifications. Products conforming to the American Society for Testing and Materials (ASTM) specifications assure users of the fabric's quality and suitability for rigorous applications. Such compliance not only certifies strength and performance but also boosts confidence among engineers and architects relying on standardized materials for their projects.
Trustworthiness in welded wire fabric is reinforced by its proven track record in numerous landmark construction projects worldwide. Engineers and construction managers repeatedly choose WWF due to its milled precision and enduring performance, adding layers of reliability to their projects. The ability of welded wire fabric to withstand environmental stresses, such as temperature changes and moisture exposure, ensures that structures remain safe and secure over time. Moreover, manufacturers often back their products with warranties and dedicated support, further enhancing trust among users and stakeholders.
In summary, welded wire fabric represents a convergence of experience, expertise, authoritativeness, and trustworthiness within the construction reinforcement sector. Its application continues to evolve with advancements in engineering practices, setting it apart as a preferred choice for modern infrastructure development. As the construction industry pivots towards more sustainable and efficient practices, welded wire fabric stands out not only as a reinforcement solution but as a testimony to innovation in building materials. Its influence and adaptability underscore its critical role in shaping the skyline of cities and the robustness of critical infrastructures globally.