Welded wire fabric 4x4, often considered a staple in construction and industrial settings, is gaining attention for its myriad benefits and applications. As an expert in the field of construction materials, sharing insights on this versatile product can extend its reach and maximize its utility in various projects.
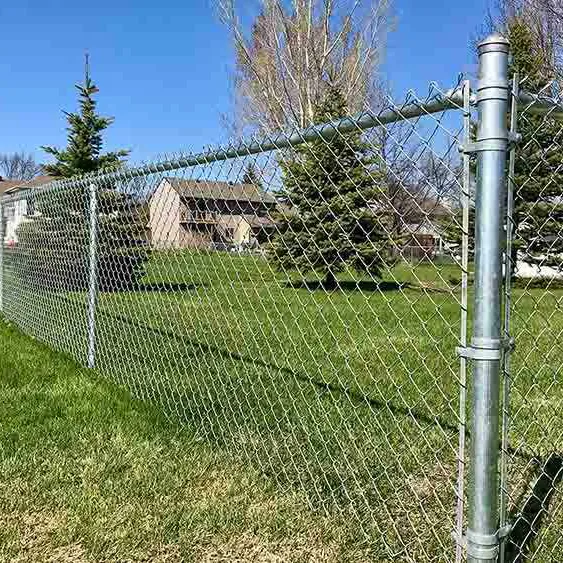
Welded wire fabric, abbreviated as WWF, specifically in the 4x4 configuration, refers to the grid of steel wires welded at intersections to form a flat sheet with regular square gaps measuring 4 inches by 4 inches. It is primarily used in reinforcing concrete, a critical process ensuring structural strength and stability. Professionals recognize its capability to bear loads and resist tension, making it an essential component in constructing driveways, pavements, and building foundations.
One of the distinguishing features of the 4x4 welded wire fabric is its ease of installation. The uniform grid pattern accelerates the laying process, cutting down labor time significantly compared to manually tied rebar. This efficiency benefits contractors aiming to optimize project timelines without compromising on quality. The reliability and consistency of welded wire fabric minimize human errors often encountered in traditional reinforcement methods.
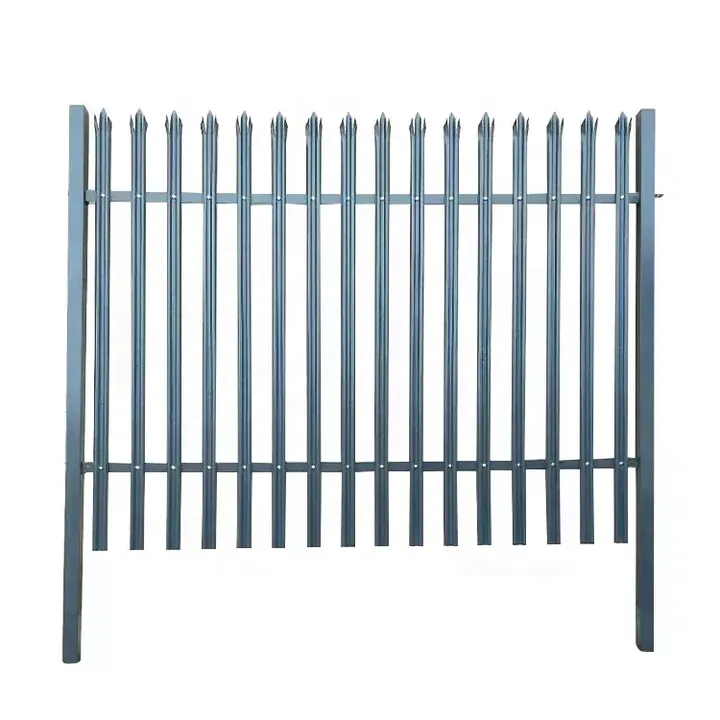
Beyond straightforward applications, the 4x4 specification is instrumental in innovative architectural designs. Its adaptability allows it to conform to various shapes and forms, meeting diverse aesthetic and functional demands. For instance, in landscape design, welded wire fabric can be used creatively to support rock walls or gabions, adding both an artistic and practical element to outdoor spaces.
From an expertise standpoint, acknowledging the manufacturing process brings further appreciation of this material. The production involves precision welding of wires made from low-carbon steel under strict quality controls. These standards ensure the fabric's durability and resistance to environmental factors such as moisture, which can cause rust and weaken structural integrity. Enhanced coatings like galvanization further improve its lifespan, offering longevity in diverse weather conditions.
welded wire fabric 4x4
Authoritativeness in discussing 4x4 welded wire fabric also stems from recognizing its standards compliance. Most of these products meet ASTM (American Society for Testing and Materials) specifications, ensuring that the wire diameter and the tensile strength are up to code. This compliance gives architects, engineers, and builders confidence in the material's performance, affirming its place as a trusted component in construction.
In terms of trustworthiness, users of welded wire fabric consistently report satisfaction in meeting both safety and structural benchmarks. Testimonials from industry leaders highlight reduced risks of cracking and shifting in concrete work, thanks to the reinforcement provided by WWF. Moreover, its application reduces the long-term maintenance cost of buildings and infrastructure, appealing to property developers aiming for economic efficiency.
The sustainability aspect further enhances the trust in 4x4 welded wire fabric. Its steel composition makes it recyclable, aligning with modern environmental goals in construction. By choosing WWF, projects can significantly reduce their carbon footprint, contributing to sustainable building practices.
In conclusion, welded wire fabric 4x4 serves as a testament to innovation in construction materials. Its efficiency, adaptability, compliance with standards, and environmental benefits make it a superior choice for anyone involved in construction and architecture. For professionals looking to enhance the quality and sustainability of their projects, understanding and utilizing this robust material is a step forward in creating enduring and responsible structures.