The welded wire fabric (WWF) market has witnessed a significant fluctuation in pricing over the past few years. Understanding these price dynamics requires delving into several factors that can influence costs, including raw material prices, manufacturing processes, global demand, and supply chain logistics.
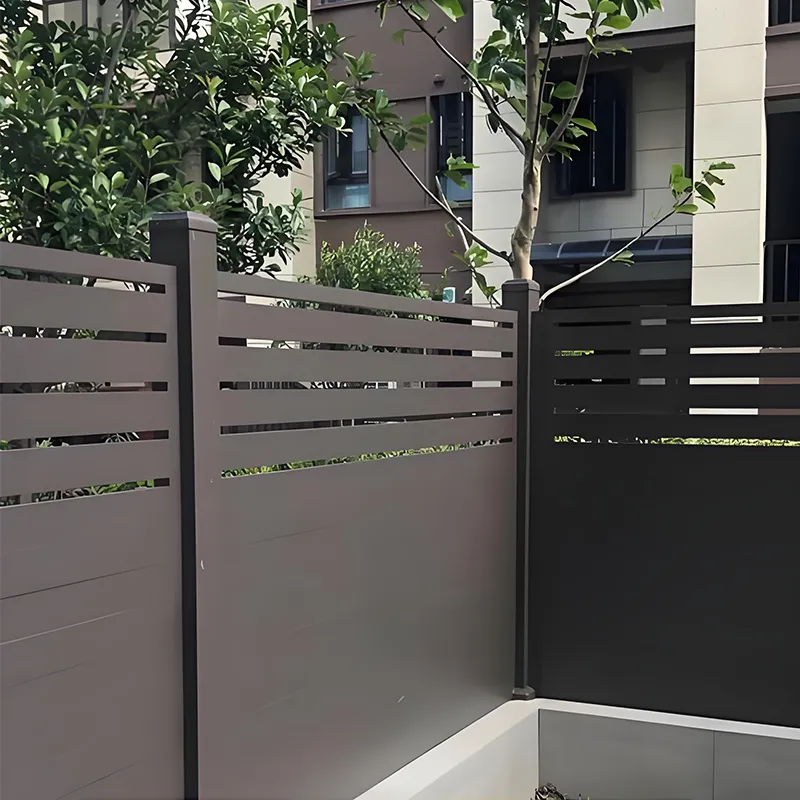
Welded wire fabric, often utilized in construction projects for its strength and durability, is composed primarily of steel, which is subject to global market trends. The price of steel has been fluctuating due to varying factors such as geopolitical events, trade policies, and production capacities in major steel-producing countries like China and the United States. For instance, tariffs on imported steel can cause domestic prices to rise, directly affecting the cost of welded wire fabric production.
Moreover, the manufacturing process itself is integral to the final cost of welded wire fabric. It involves specific machinery and skilled labor to ensure the precise welding of wires into a grid-like structure. This process is energy-intensive, and any fluctuations in energy costs can impact pricing. Manufacturers must continuously invest in updated technology and training to maintain efficiency and quality, which can contribute to the overall cost.
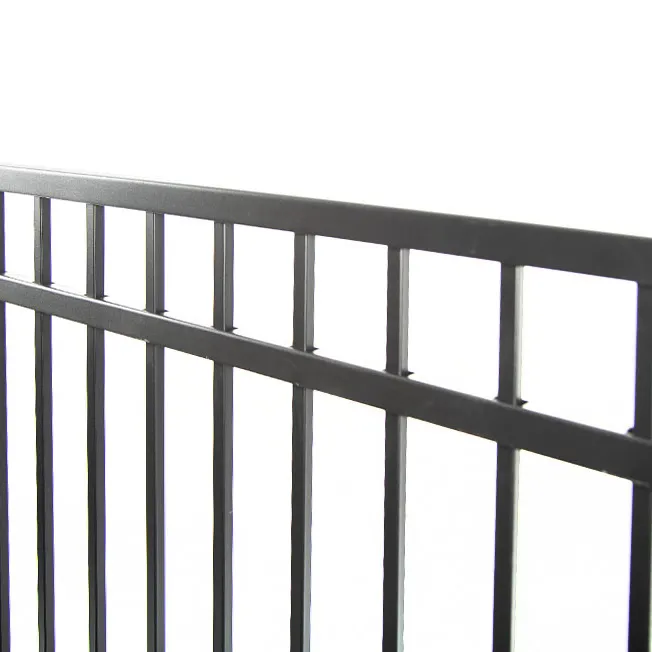
The global demand for construction materials has been on the rise as urbanization and infrastructure development continue to escalate worldwide. Countries are investing heavily in new projects, leading to a surge in demand for materials like welded wire fabric. This increased demand can drive up prices, especially in regions where supply cannot keep pace.
Supply chain logistics also play a critical role in the cost of welded wire fabric. Disruptions in transportation, whether due to natural disasters, pandemics, or geopolitical tensions, can result in delays and increased shipping costs, all of which are passed on to the consumer. Additionally, the sourcing of raw materials from distant locations can further convolute the supply chain, creating potential for additional costs or delays.
welded wire fabric price
Despite these challenges, several strategies can be implemented to manage welded wire fabric costs effectively. Suppliers and consumers can enter into long-term contracts to stabilize prices over a set period, minimizing the impact of market volatility. Additionally, investing in local production facilities can reduce dependency on imported materials and mitigate the risks associated with long supply chains.
It's also crucial for companies to keep abreast of the latest technological advancements in welded wire fabric production. Innovations such as automated welding systems can improve efficiency, lower labor costs, and reduce the likelihood of human error, thereby potentially lowering overall production costs. Implementing sustainable practices, such as recycling steel or utilizing renewable energy sources, can not only contribute to environmental conservation but also offer cost savings in the long term.
Another key aspect is the trustworthiness and reputation of suppliers. Engaging with reputable suppliers who have established a dependable supply chain and consistent pricing strategies is paramount. Suppliers that offer transparent pricing models and are willing to share information on market trends and potential disruptions can be invaluable partners.
In summary, while the price of welded wire fabric is influenced by a myriad of factors ranging from raw material costs to global demand and supply chain logistics, strategic planning, and partnerships can help mitigate these impacts. Companies must stay informed about market conditions, invest in efficient technology, and choose reliable suppliers to ensure they receive quality products at competitive prices. By doing so, they can maintain their project budgets and timelines, ultimately contributing to successful construction outcomes.