Welded wire fabric sizes play a critical role in multiple construction and agricultural applications. When determining the right size for your project, numerous factors come into play, such as load-bearing capacity, usage environment, and specific application needs.
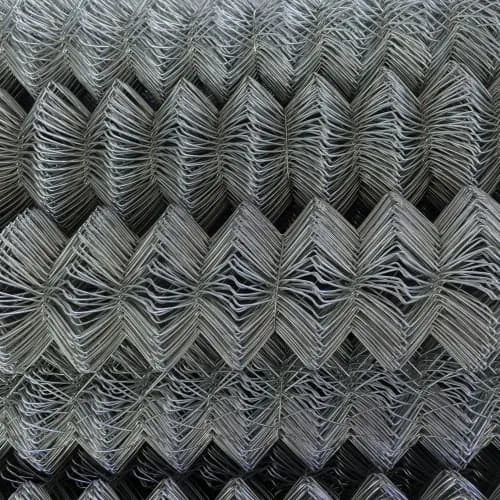
Experience in the construction sector highlights that selecting the appropriate welded wire fabric size is not a one-size-fits-all solution. Each project requires critical assessment regarding the needed mesh size, wire gauge, and material composition. For instance, in concrete reinforcement, engineers might opt for heavier gauges, like 6 or 8, ensuring robustness and structural integrity under substantial loads.
Expertise in material specifications can significantly influence the effectiveness of the application. For perimeter fencing in agricultural settings, lighter gauges such as 10 or 12 often suffice, given they deter livestock without excessive strength that might compromise flexibility and ease of installation. The choice of welded wire fabric size can therefore directly impact both the initial installation costs and the long-term durability of the fence.
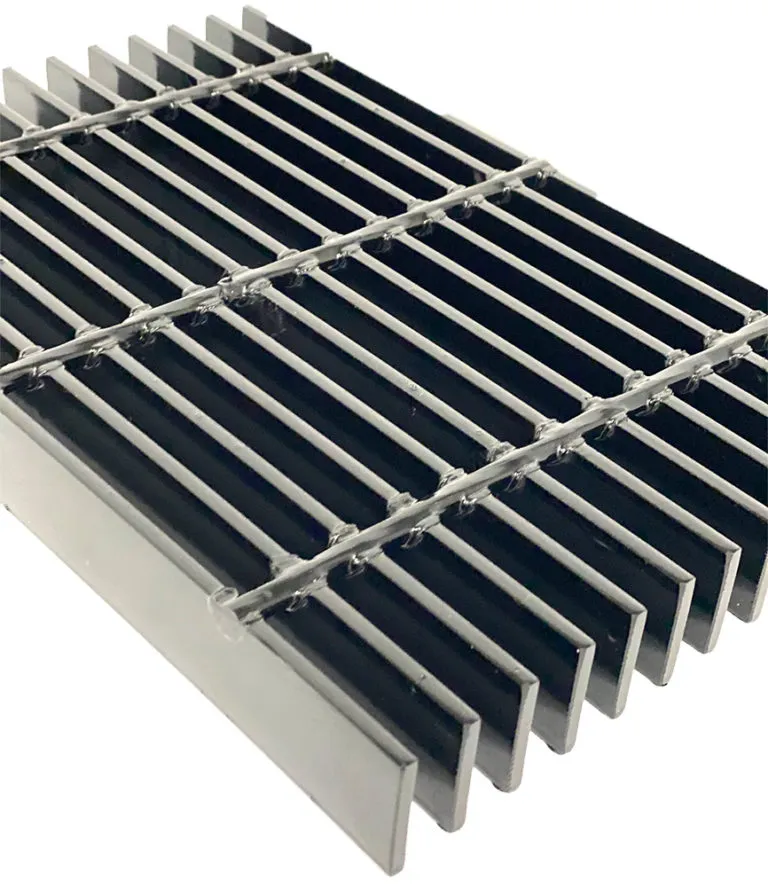
Authoritativeness in construction guidelines and engineering practices further underscores the importance of standard compliance. When adhering to construction codes, fabric sizes must align with ASTM standards or specific local regulations to ensure safety and efficacy. An engineer must consult these standards diligently to verify that the selected welded wire fabric size will function correctly for its intended use, whether it’s supporting soil erosion control or serving as a plaster mesh in subdivisions.
welded wire fabric sizes
Trustworthiness is paramount. Partnering with certified suppliers of welded wire fabric who guarantee that their products comply with industry standards can avert unnecessary project risks. Genuine certification provides assurance that the wire mesh has undergone rigorous testing to meet pressures of specific environmental conditions and mechanical stressors. This credibility is what differentiates a successful, long-lasting project from one plagued by continual maintenance challenges.
The decision-making process also involves technological advancements in manufacturing. Modern innovations allow for improved corrosion resistance through galvanized or PVC-coated wire, which could affect size choices. In coastal projects, where salinity is a factor, these adaptations are essential for prolonging lifespan and maintaining structural function. Engineers must weigh the benefits of these enhancements against cost and project requirements.
In practice, deciding on the size of welded wire fabric tilts on the balance of theory and empirical assessments. Field tests and past project insights offer invaluable knowledge. For instance, empirical data may suggest that a particular project warrants a specific mesh opening size to maximize tensile properties while minimizing material use. Site-specific conditions, such as soil composition and weather exposure, also necessitate customization that prefabricated standards might not cover.
Ultimately, the perfect fabric size for a project cannot be determined without a multifaceted approach that considers experience and expertise, backed by authoritative resources and trustworthy partnerships. This strategic selection process not only ensures compliance with safety standards but also optimizes the utility and longevity of the welded wire fabric in its application.