Understanding the costs associated with welded wire mesh per square foot involves a blend of material science, structural engineering, and market dynamics. By leveraging expertise and real-world insights, one can gain a comprehensive understanding of this critical component in construction and several other industries.
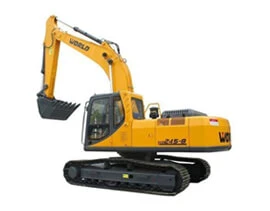
Welded wire mesh, an essential product for construction and industrial applications, offers versatility and strength. It is used in concrete reinforcement, fencing, and even artistic installations. The cost per square foot is influenced by various factors, including the type of material used, the size of the mesh, the coating, and prevailing market trends.
A primary driver of cost is the type of metal involved. Steel, the most commonly used material in welded wire mesh, varies in price due to fluctuations in global steel markets. Galvanized steel is often chosen for its corrosion resistance, which adds to the cost due to the zinc coating process. Stainless steel options, while more expensive, are sought after for their exceptional durability and resistance to rust, making them ideal for high-exposure environments.
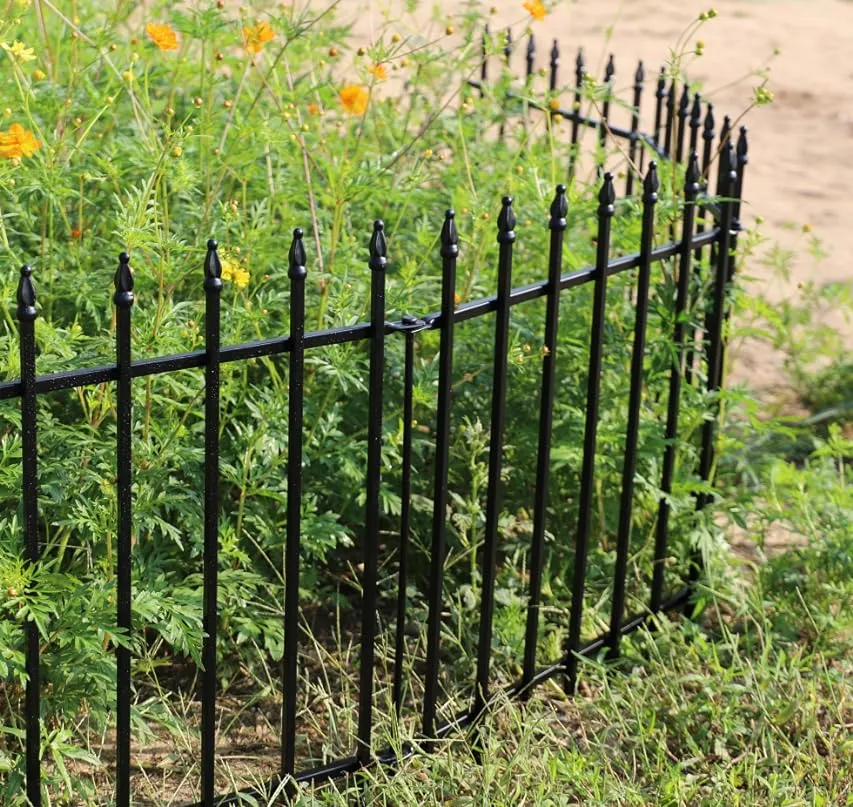
Mesh size and wire diameter also play significant roles in cost determination. Larger mesh sizes with thinner wires tend to be less expensive due to reduced material use. Conversely, smaller mesh sizes with thicker wires demand more resources, thus increasing the cost. Buyers need to balance the structural needs of their projects with budget constraints, making mesh size an essential consideration.
Coatings and finishes further influence costs. PVC-coated meshes provide additional durability and aesthetic appeal, beneficial in applications ranging from aviaries to decorative partitions. This coating adds another layer of expense, but the long-term benefits often justify the initial investment, especially in corrosive environments.
welded wire mesh cost per square foot
Real-world market conditions add another layer of complexity to the cost structure of welded wire mesh. Transportation costs, supply chain disruptions, and local demand can all impact prices per square foot. Engaging directly with manufacturers or authorized distributors often yields more competitive pricing and insight into potential market shifts.
Experts in the field suggest that while upfront costs are critical, the lifetime value and suitability of the mesh for specific applications are equally important. Durability, maintenance, and aesthetic values can all translate to cost savings over time, particularly in large-scale projects.
Manufacturers and vendors such as XYZ Steel Solutions and ABC Infrastructure provide detailed product specifications and pricing models, reinforcing the importance of selecting a reputable supplier. Their expertise and field studies have shown that investing in higher-quality mesh can reduce replacement frequency and project downtime, aligning with both economic and operational efficiencies.
For those sourcing welded wire mesh, it's prudent to conduct a thorough needs assessment. Understanding project requirements, environmental conditions, and expected load capacities ensures that the selected mesh type offers optimal functionality. Consulting with industry professionals provides additional assurance that the specifications meet both budgetary and structural needs.
In conclusion, determining the cost per square foot of welded wire mesh is not merely a numerical exercise but a strategic evaluation of quality, performance, and economic factors. By considering these elements, decision-makers can optimize their investments, achieving both short-term cost-efficiency and long-term project success. Each selection must be informed by a combination of expert advice, material science knowledge, and market trends to fully realize the benefits of welded wire mesh in various applications.