Welded wire mesh has long been recognized as a formidable ally in the construction industry, particularly when it comes to bolstering concrete slabs. For decades, contractors, engineers, and construction specialists have relied on this material for its unrivaled combination of durability and flexibility, making it indispensable for projects demanding strength and stability.
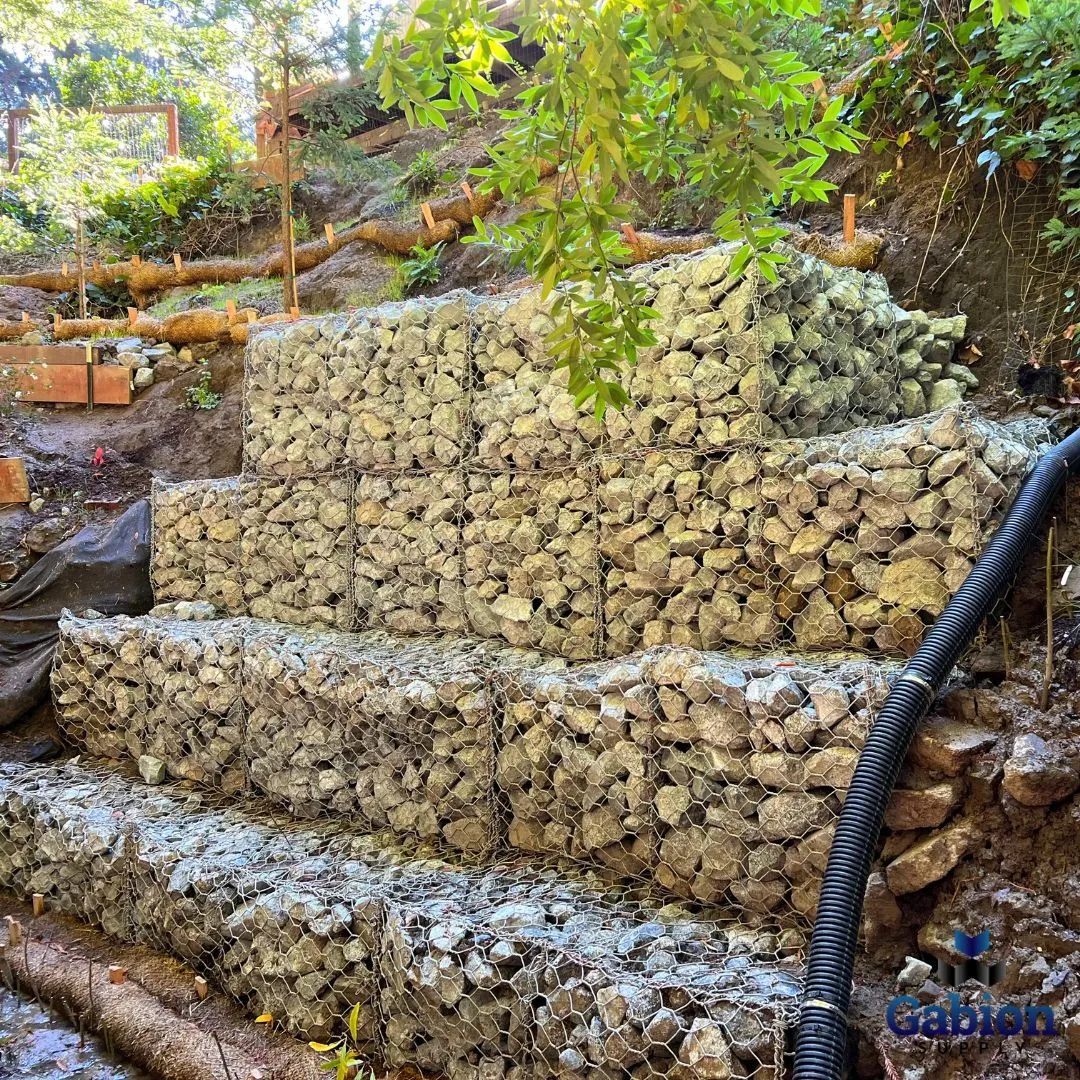
The secret of welded wire mesh lies in its meticulous construction process. Comprising a network of longitudinal and transverse wires welded at intersections, this mesh forms a grid pattern capable of distributing loads across a broad area. This distribution is crucial for concrete slabs, as it helps prevent concentration of stress at specific points, ultimately reducing the risk of cracking and structural failure. Its use in concrete slabs enhances tensile strength, ensuring long-term performance and resilience against environmental stressors.
From a practical standpoint, using welded wire mesh in concrete slabs offers significant time and cost benefits on construction sites. Unlike traditional rebar, which requires labor-intensive tying and positioning, welded wire mesh is faster to lay out and position. Its prefabricated nature means construction teams can significantly accelerate project timelines, thereby reducing labor costs and minimizing onsite errors. This efficiency does not compromise quality, as the precision of machine-welded wires ensures consistent spacing and alignment, essential for uniform load distribution.
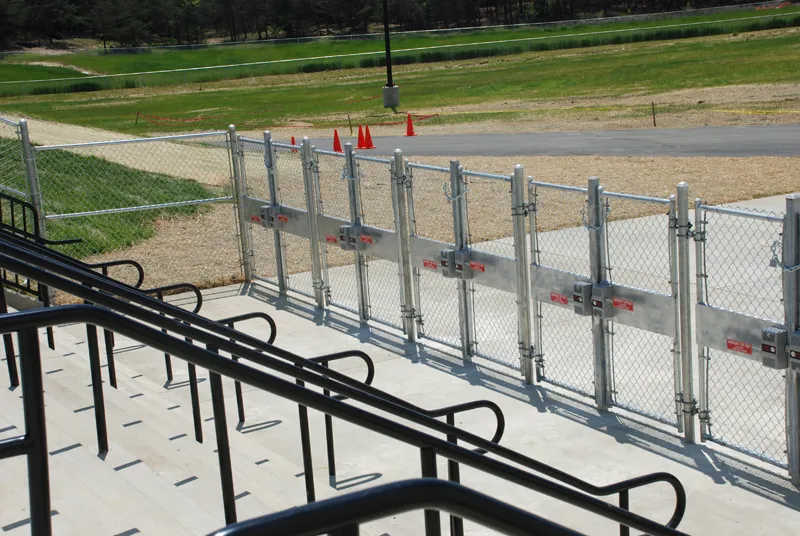
For engineers, welded wire mesh provides the flexibility needed to customize designs according to specific structural needs. Whether employed in residential foundations or expansive commercial flooring systems, this material can be tailored in terms of wire diameter, spacing, and grid size to meet diverse project demands. This versatility is paramount for optimizing the structural integrity and performance of concrete slabs across various applications.
welded wire mesh for concrete slabs
In terms of environmental impact, welded wire mesh stands out as an eco-friendly material due to its high recyclability. As the construction industry moves towards sustainable practices, materials that can be efficiently recycled without loss of quality become increasingly valuable. Using welded wire mesh aligns with green building standards, promoting environmental stewardship without sacrificing strength or reliability. Its production also involves fewer emissions compared to other reinforcing materials, contributing to a smaller carbon footprint.
Expertise in deploying welded wire mesh within concrete slabs involves understanding both material specifications and site conditions. To maximize effectiveness, experts recommend quality control measures, such as ensuring that the mesh is positioned correctly and fully embedded within concrete to prevent exposure to corrosive elements. Further, selecting the appropriate gauge and spacing of the mesh based on the projected loads and environmental conditions is crucial for maintaining structural integrity.
Adhering to industry standards and best practices reinforces the trustworthiness of using welded wire mesh in concrete construction. Compliance with guidelines established by authoritative bodies like the American Concrete Institute (ACI) or British Standards (BS) assures that welded wire mesh not only meets but often exceeds required safety and performance metrics. These guidelines provide engineers with frameworks to ensure that installations are carried out safely, reliably, and effectively, fostering confidence in the long-term viability of the structures built.
For those involved in construction—from project managers to field workers—leveraging welded wire mesh for concrete slabs is an experience built on a foundation of reliability, efficiency, and sustainability. Its track record in successfully fortifying infrastructures around the globe speaks volumes of its authority in the construction industry. With continued advancements and innovations, welded wire mesh remains a cornerstone of modern construction practices, offering unquestionable credentials in strength, efficiency, and eco-consciousness.