Exploring the intricacies of welded wire mesh sheet sizes unveils a realm of nuances that speak directly to quality, efficiency, and application optimization. As a cornerstone in the realm of construction, industrial, agricultural, and commercial applications, understanding welded wire mesh sheet sizes is pivotal for engineers, architects, and procurement experts, driving both performance and cost-effectiveness.
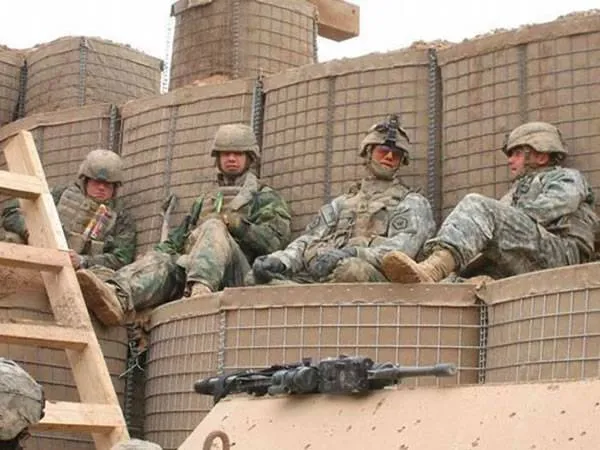
Welded wire mesh sheets are meticulously crafted through a process of intersecting wires that are electrically welded at the intersections to form a grid. The specificity in choosing the right mesh size can greatly influence the success of a project. The variation in sheet sizes accommodates a plethora of applications, from reinforcing concrete structures to creating secure fencing barriers, thereby emphasizing the necessity for precision in selection.
Experience
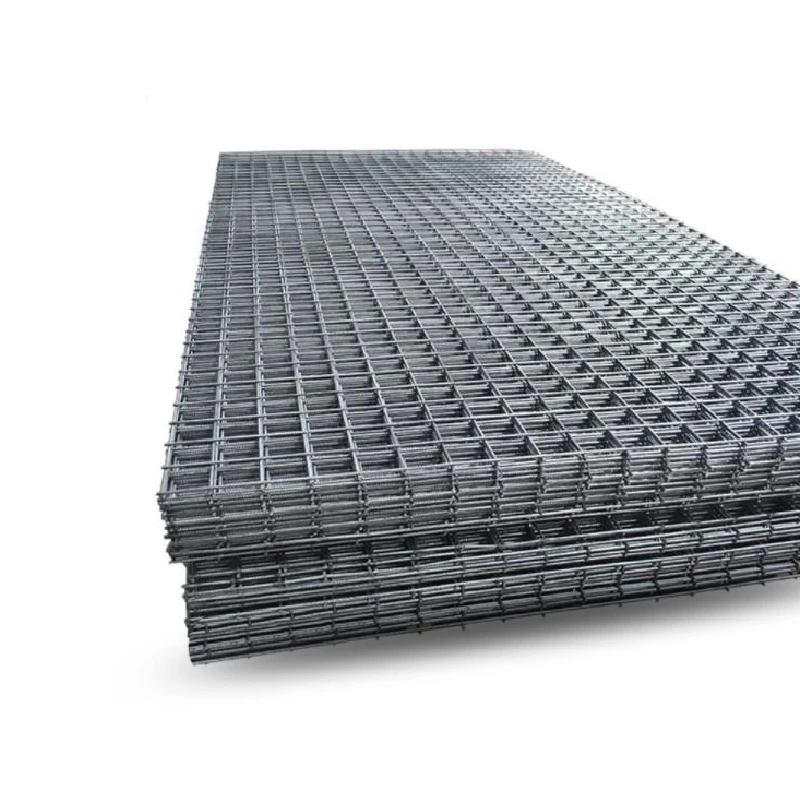
Delving into field experiences, seasoned construction managers reveal that the efficiency of installation and the longevity of the application heavily depend on selecting the appropriate welded wire mesh sheet size. For instance, in urban high-rise construction, the use of thicker wire diameters with tighter mesh spacing ensures enhanced structural integrity. Projects that adapted a keen eye for mesh size optimization reported up to a 20% increase in materials efficiency, reduced waste, and minimized post-construction adjustments. These insights indicate that firsthand experience with the material compounds success in implementation.
Expertise
The domain of welded wire mesh is enriched with technical specifications that require an expert understanding. Standardized mesh sizes usually range from 1/4 inch to several inches between wires, influencing both load capacity and permeability. Each application dictates specific sizes; for instance, smaller mesh sizes are paramount in window screens or animal enclosures, preventing pests or ensuring containment. Structural applications, such as in concrete reinforcement, commonly employ larger mesh sizes such as 6x6 inches, to aid in the distribution of load and prevent cracking. Engineers often calculate specific mesh requirements based on load calculations and environmental factors to ensure robustness and compliance with industry standards.
welded wire mesh sheet sizes
Authoritativeness
Authoritative insights come from adherence to industry standards set forth by organizations such as ASTM International, which provides guidelines on the manufacture and quality of welded wire fabrics. Adopting standards like ASTM A1064/A1064M assures buyers and users of the compliance and integrity of the mesh used. Suppliers and manufacturers who consistently meet or exceed these benchmarks have established trust and reliability, becoming the go-to source for projects requiring precision and quality assurance.
Trustworthiness
Trust in a product extends beyond certification; it involves a transparent manufacturing process, ethical sourcing, and consistent performance reviews. Suppliers proactively engaging with third-party testing and acquiring certifications not only enhance credibility but affirm the trust purchasers place in the product longevity and safety. Documented case studies and client testimonials act as powerful testimonies to the reliability of a supplier and the effectiveness of specific mesh sizes across various applications.
In summary, understanding welded wire mesh sheet sizes transcends basic selection; it is an intersection of experience, expertise, authority, and trust. Selecting the right sheet size enhances project quality, ensures compliance with safety standards, and optimizes economic output.
As applications for welded wire mesh continue to evolve, so too must the understanding of its fundamental intricacies. Embracing a comprehensive approach integrates not only technical specifications but also the broader spectrum of effects influenced by precise mesh size selection, paving the way for more resilient, efficient, and innovative applications in numerous industry sectors.