Selecting the right welded wire mesh for a project involves an intricate blend of size, weight, and application specifics. Though overlooked often by novices, precision in these components can spell the difference between a robust structure and an engineering mishap. With years of experience working in construction and material sourcing, the intricacies of welded wire mesh are as nuanced as the projects they build.
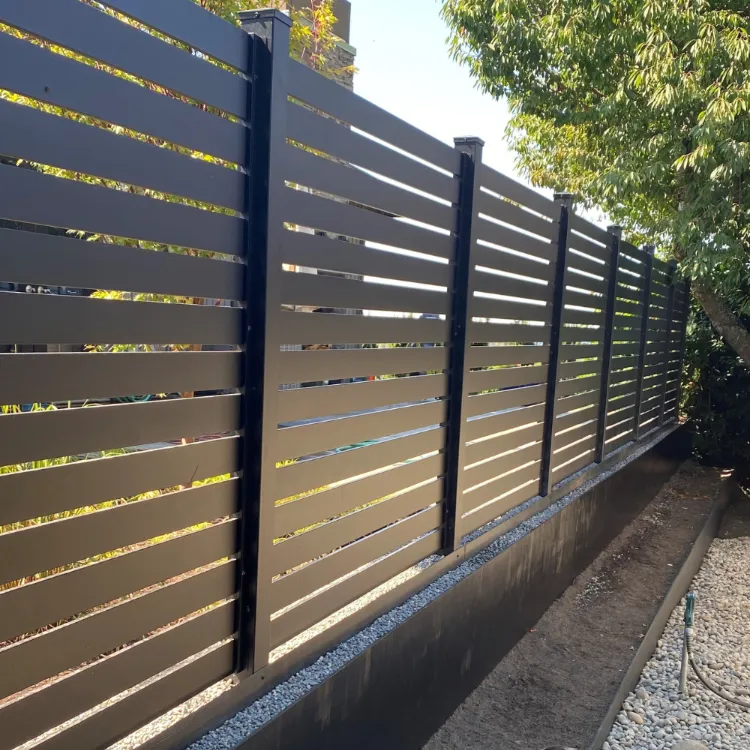
A welded wire mesh is a key structural component employed in various applications, from simple animal cages to intricate construction projects. Understanding the sizes and weights is critical for architectural stability, effectiveness, and budget management.
When it comes to sizes, welded wire mesh typically features a grid-like pattern where the intersecting wires are welded at each junction. The size of this grid varies significantly with application requirements. For instance, fine mesh sizes, such as 1/4 inch by 1/4 inch, are more suitable for small animal enclosures or projects demanding substantial detail and precision. Larger mesh sizes, like 6 inches by 6 inches, are often employed in construction for reinforced concrete elements—these larger grids support greater weight and reduce material costs due to wider spacings. The choice of mesh size directly impacts the application—smaller meshes mean higher material density and rigidity, effectively supporting more delicate uses, while larger meshes are paramount for their economic and structural benefits in large-scale applications.
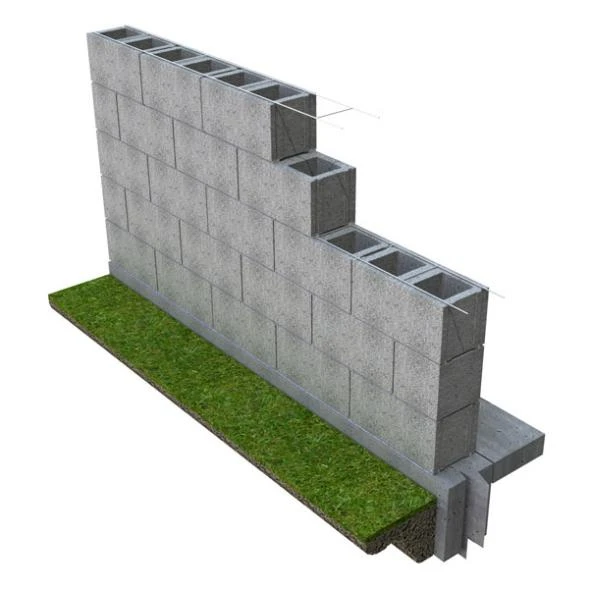
Weight is another crucial factor tightly interlinked with mesh size. The wire gauge, which dictates the thickness of the wire used, plays a pivotal role in defining the weight of the mesh. Lower gauge numbers indicate thicker wire and, therefore, a heavier mesh. This weight has direct implications on the durability and strength of the welded wire mesh. For instance, a 10-gauge mesh would be significantly heavier and stronger than a 16-gauge equivalent. Such sturdiness is indispensable for heavy-duty applications such as road reinforcement, where the mesh must support not just the overlaying material but also the stress of vehicles traversing it. Conversely, a higher gauge mesh, with its reduced weight, wins favor for lightweight applications where ease of transport and manipulation is prioritized over brute strength.
welded wire mesh sizes and weights
The balance between size and weight in selecting welded wire mesh is not merely about fulfilling basic needs, but optimizing each application for cost-effectiveness and future longevity. Purchasing decisions should also weigh environmental conditions, corrosion potential, and specific structural responsibilities. Opting for galvanized options, for instance, imparts corrosion resistance, ensuring longevity in outdoor or moisture-prone environments.
With these dynamics in play, expertise becomes invaluable. Over the years, professionals like myself have relied on the astute selection of welded wire mesh sizes and weights to ensure project success. It's more than understanding dimensions and heft; it's about leveraging this knowledge to engineer solutions that offer resilience, efficiency, and durability. For practitioners in construction and engineering, adeptly wielding this knowledge is not merely advantageous—it is essential.
Ultimately, engaging with trusted suppliers who offer detailed spec sheets and testimonials of their welded wire mesh products can enhance this technical know-how. These partnerships foster an environment where innovation meets reliability, advancing projects from mere blueprints to exceptional structural achievements, grounded in expertly chosen welded wire mesh configurations.