Understanding the significance of welded wire mesh sizes is crucial for anyone involved in the construction, agriculture, or industrial sectors. This comprehensive guide delves deep into the world of welded wire mesh, unraveling its dimensions, applications, and the benefits of selecting the appropriate size for your specific needs.
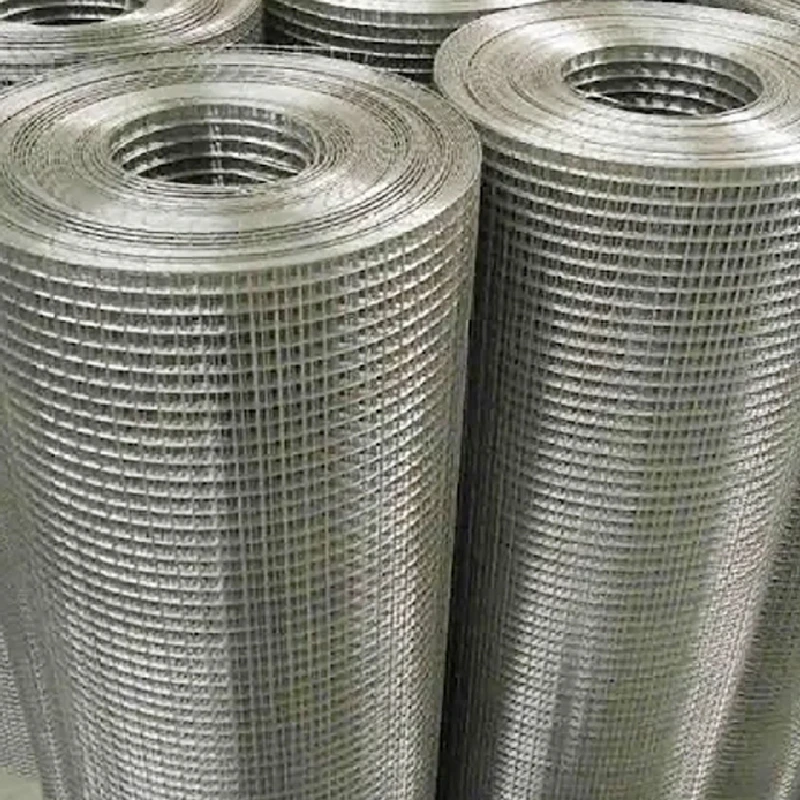
Welded wire mesh is a versatile material composed of intersecting steel wires joined by welding to form a grid-like structure. Its widespread application ranges from reinforcing concrete to creating enclosures for animals, and even serving as trellises for climbing plants in agriculture. The selection of mesh size is a decision that hinges on factors such as application, required strength, and exposure to elements.
Mesh size refers to the dimensions of the grid created by the intersecting wires and is typically represented by the spacing between wires (in inches or millimeters). It’s vital to not just consider the size of the openings but also the gauge or thickness of the wire. For instance, a heavier gauge wire provides greater strength and security, while a lighter one offers flexibility and cost-effectiveness.
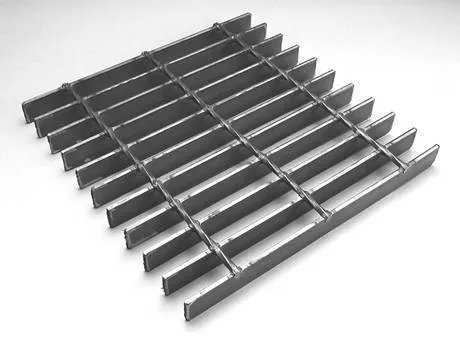
For construction purposes,
welded wire mesh serves as a reinforcement to concrete slabs and structures. Choosing an appropriate mesh size prevents cracking and enhances the integrity of the structure. Builders often opt for 6x6 or 4x4 inch mesh size intervals with wire gauges ranging from 6 to 10. This choice supports the weight and distribution of concrete without compromising stability.
In agriculture, the needs differ significantly. When constructing enclosures for livestock or poultry, smaller mesh sizes like 1x1 or 2x2 inches are preferred, combined with medium to heavy gauge wires to ensure both visibility and security from predators. This mesh not only contains the animals but also seamlessly integrates with the environment, ensuring airflow and visibility.
welded wire mesh sizes chart
The industrial sector, known for its demanding applications, often requires custom sizes. For example, in constructing machine guards, a balance between safety and visibility is vital; therefore, smaller gauges and thicker wires are recommended. Custom welded wire solutions cater to exact specifications, ensuring optimal performance and safety.
Purchasing welded wire mesh requires careful consideration of factors such as corrosion resistance, tensile strength, and adaptability to environmental conditions. Galvanized or PVC-coated wire meshes are excellent choices for wet or corrosive environments, offering durability and longevity. Consulting an experienced supplier or expert who understands your specific requirements not only ensures quality but also offers insights into innovative applications or potential pitfalls.
Quality assurance is non-negotiable in sectors relying heavily on welded wire mesh. Expertise in manufacturing and sourcing guarantees product integrity, supported by industry certification and testing. Reliable suppliers offer transparency in material composition, often providing test results and industry-standard compliance.
Trustworthy advice from seasoned professionals in the field is invaluable when selecting the right welded wire mesh size. Their experience and understanding of market trends, materials, and technological advancements can guide purchasing decisions that balance cost efficiency with performance.
In conclusion, understanding welded wire mesh size charts isn't just about picking a dimension off a chart; it's about tailored solutions that meet and exceed application demands. As industries evolve, the mesh's role adapts, continuously offering innovative, reliable, and efficient solutions. Whether in construction, agriculture, or industry, the informed selection of welded wire mesh guarantees the fulfillment of project objectives with precision and confidence.