Understanding the intricacies of welded wire reinforcement (WWR) sizes can significantly enhance construction endeavors, boosting both efficiency and quality. With a deep diving into the specifics, this article aims to unwrap the technicalities and the practical implications of WWR, creating a resource that bridges the gap between foundational knowledge and expert advice.
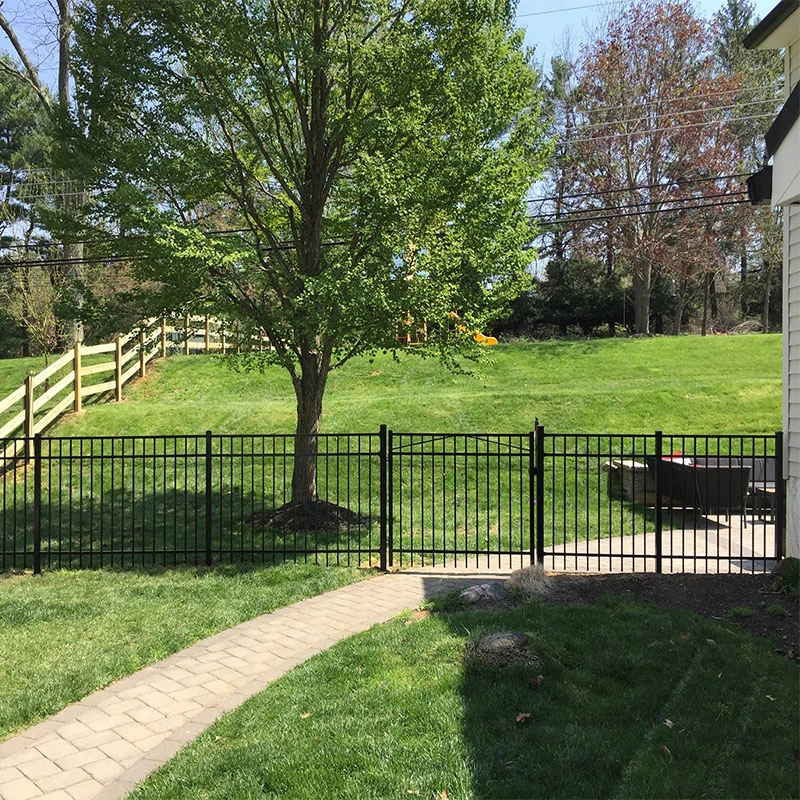
Welded wire reinforcement is a robust and versatile material widely used in reinforced concrete applications. It is employed in construction projects ranging from industrial infrastructures to residential buildings. Its primary function is to bolster concrete’s tensile strength, helping structures endure various stresses. One of the most critical aspects of WWR is understanding its sizes and how they impact the overall project outcome.
Each WWR mat is made from intersecting wires welded together to form a grid. The size of these grids directly correlates with the reinforcement's strength and flexibility. Typically, WWR is denoted by two indices one for longitudinal wires and another for transverse wires. For instance, a 6x6 W1.4xW1.4 indicates a grid where wires are spaced 6 inches apart, both longitudinally and transversely, with each wire having a cross-sectional area of 1.4 square inches.
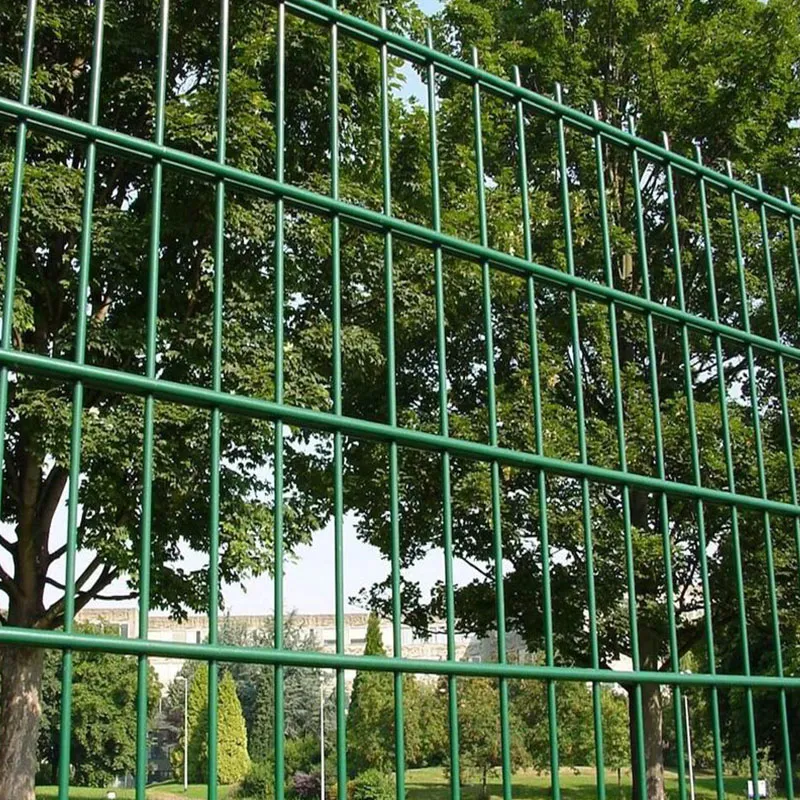
Choosing the right wire size and grid spacing is paramount. Engineers and builders must consider factors like load-bearing needs, environmental conditions, and structural design. Larger mesh sizes, like 12x12, offer more flexibility and are often used in slabs where reduced load is an advantage. Conversely, tighter grids with thicker wires are suitable for projects requiring added strength, such as in retaining walls or structural flooring.
From an experience standpoint, the practical application of different WWR sizes cannot be overstated. Successful projects often share a common thread alignment with structural demand.
Imagine a scenario where a bridge deck requires reinforcement. Opting for the wrong wire size could lead not only to potential structural failure but also to financial loss. Engineers with years of experience in the field emphasize the critical nature of these decisions, advocating for precise calculations and consideration of each project's unique requirements.
welded wire reinforcement sizes
Expertise plays a crucial role in navigating the nuances of WWR sizes. Professionals well-versed in civil engineering and construction technology offer insights into optimizing reinforcement for durability and cost-effectiveness. Detailed analysis regarding strain distribution, seismic activity adaptation, and thermal contraction aids in refining WWR size selection, ensuring that the reinforcement serves its intended purpose without compromise.
In domains that demand high authoritativeness and trustworthiness, such as construction and engineering, accuracy in WWR size specification is a benchmark of professionalism. Building codes and standards, such as those from the American Society for Testing and Materials (ASTM), establish the baseline for what is acceptable in terms of reinforcement sizes and material quality. Compliance with these standards not only assures safety but also enhances reputability in a highly competitive industry.
Another layer of trust is built through transparency in sourcing and material consistency. Reputable providers of WWR often disclose the manufacturing processes, quality control measures, and material specifications. Such disclosure builds confidence among project managers and stakeholders, ensuring that the reinforcement used meets both legal and quality standards.
In conclusion, the world of welded wire reinforcement is intricate and requires a thorough understanding of available sizes and their implications. It demands an integration of experience, expert analysis, authoritative guidelines, and trust-centric practices. Whether revamping a railway platform or constructing a multi-story car park, choosing the correct WWR size is pivotal and manifests through enhanced performance, longevity, and structural integrity. As technology and construction methods continue to evolve, the foundational principles of proper reinforcement selection remain a steadfast constant, guiding new generations of engineers and builders towards success.