Welding steel mesh stands as a crucial component in a myriad of construction and industrial projects. Its intrinsic strength, flexibility, and durability make it indispensable, especially in reinforcing concrete structures. Understanding the nuances of welding steel mesh is essential for any firm seeking to enhance the structural integrity and longevity of their projects.
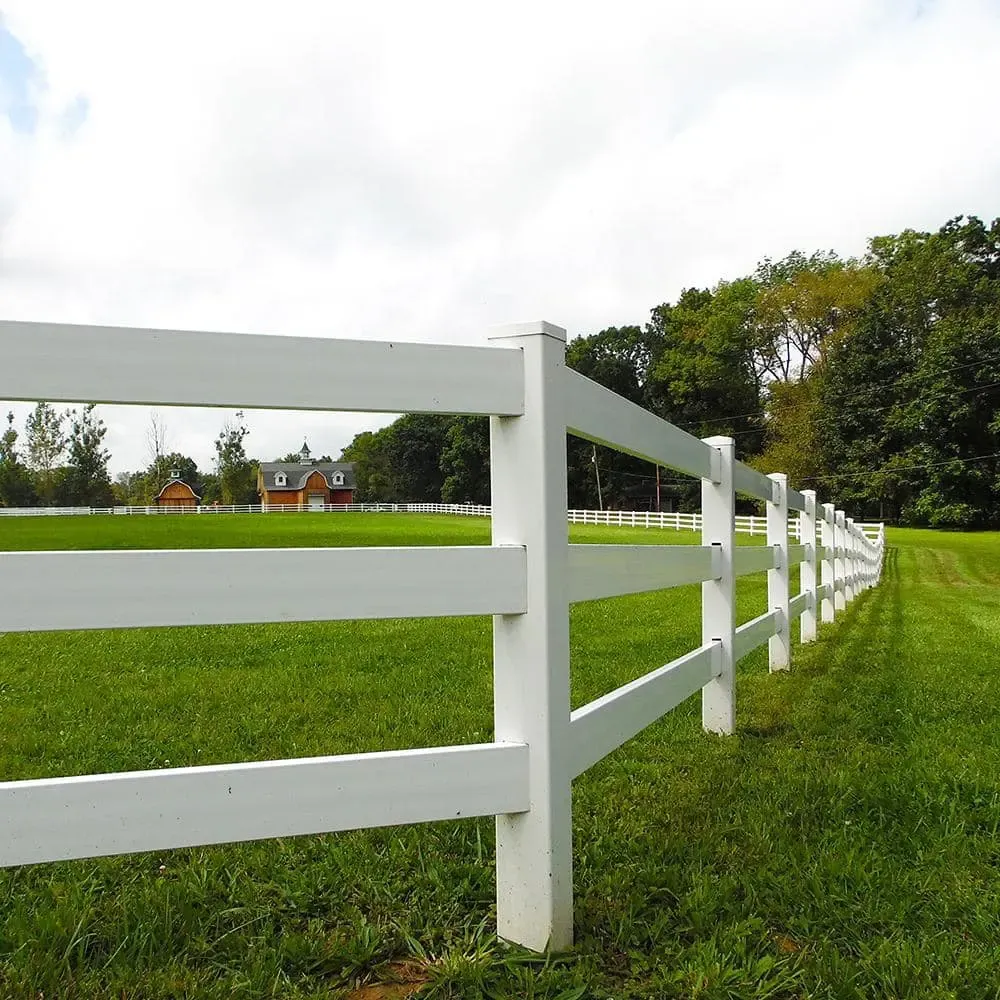
Experience in the field of steel mesh welding is paramount. Seasoned professionals often highlight the importance of choosing the right materials. High-quality steel ensures the mesh maintains its form and strength across various applications. The dimensions of the mesh play an equally pivotal role, as they must align with specific project requirements to maximize efficiency and effectiveness.
A vital aspect of welding steel mesh lies in preparation. Cleaning the steel to remove any signs of rust, oil, or dirt is fundamental. This step enhances the weld’s adhesion, ensuring a robust bond that withstands environmental and load stresses. Furthermore, precise measurement and cutting of the mesh contribute to a cohesive structure that fits seamlessly into its designated space, further augmenting the project’s stability.
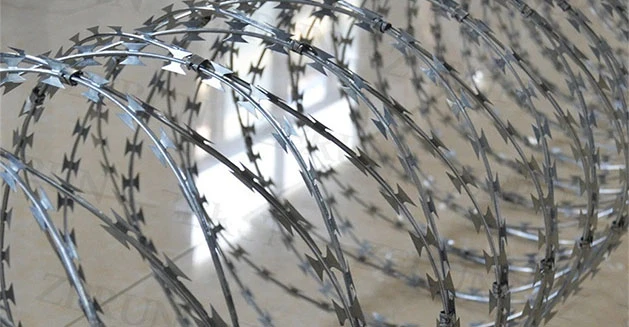
Expertise comes into play significantly when discussing welding techniques. MIG (Metal Inert Gas) welding is often recommended due to its ability to handle thin materials without extensive training. Alternatively, TIG (Tungsten Inert Gas) welding can offer more control and is ideal for intricate work. Both methods demand a steady hand and detailed knowledge of the materials involved, emphasizing the need for skilled labor.
welding steel mesh
Rapid advancements in welding technology have led to the emergence of automated welding processes. These technologies not only reduce human error but also enable large-scale production. Automation requires initial investment but often results in cost savings and improved precision over time. Companies leveraging these technologies can offer clients faster turnaround times and consistently high-quality outcomes, thereby establishing competitive advantages.
From an authoritative perspective, adherence to industry standards and regulations cannot be overstated. Compliance with standards such as ISO and AWS ensures that welding practices meet the highest safety and quality criteria. This not only legitimizes operations but also fosters trust among clients and stakeholders. Firms should strive to maintain certifications and engage in regular audits, reinforcing their commitment to excellence.
Trustworthiness is cultivated through consistency and transparency. Providing clients with comprehensive project plans, timelines, and progress updates can significantly enhance client relationships. Demonstrating a strong track record of past project successes and positive testimonials can further bolster a company's reputation in the industry. Trust is a valuable currency—and in industries like construction, where safety and reliability are non-negotiable, earning and maintaining client trust is crucial.
In conclusion, welding steel mesh requires a harmonious blend of experience, expertise, and adherence to authoritative standards. Companies must continuously adapt to technological advancements while maintaining a focus on quality and safety. By prioritizing trust and authoritative practices, firms can not only meet but exceed client expectations, establishing themselves as leaders in their domain. Emphasizing these core values in the approach to welding steel mesh not only contributes to successful project outcomes but also solidifies a company's position as a reliable and innovative player in the global market.