Understanding the intricacies of weld mesh sizes is crucial for professionals involved in construction, agriculture,
and industrial sectors. Weld mesh, a critical component in these fields, is often used for fencing, concrete reinforcement, and various other applications. The size of the mesh directly impacts its suitability for specific tasks, making it essential to choose appropriately.
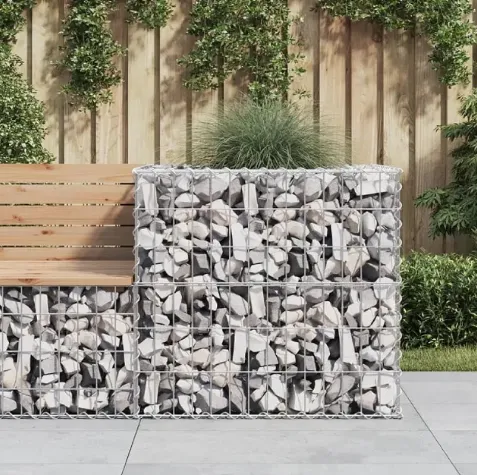
When delving into weld mesh size charts, professionals must consider multiple factors to ensure optimal performance and safety. The size chart typically provides information on the spacing of wires, the thickness of the wire, and the dimensions of the mesh panels. Each of these parameters affects the strength, flexibility, and cost of the mesh, thereby influencing the choice for specific projects.
Wire thickness, expressed in gauge or millimeters, plays a significant role in determining the durability of the mesh. Thicker wires provide enhanced strength and are ideal for high-stress applications such as security fencing or heavy-duty animal pens. However, increased thickness may also result in reduced flexibility and higher costs. Therefore, it's essential to balance strength requirements with budget constraints and the intended application.
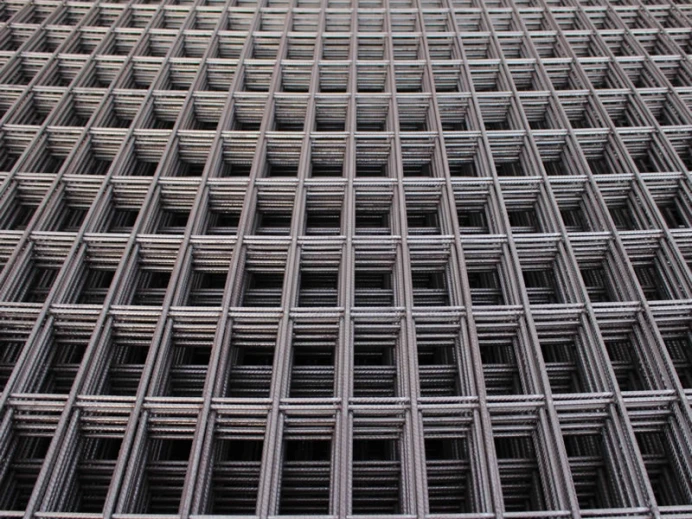
The spacing of the wires, often dictated by industry standards or specific project requirements, affects the permeability and security of the mesh. Tight spacing, such as 1/2 inch by 1/2 inch, offers superior security and is suitable for high-risk areas where intrusion prevention is paramount. On the other hand, larger spacing, like 2 inches by 2 inches, is more appropriate for agricultural use, allowing for better visibility and airflow while containing animals.
Mesh dimensions are another critical factor, with standard sheet sizes providing convenience but necessitating customization for projects requiring specific measurements. Professionals benefit from suppliers who offer tailored solutions, ensuring the mesh fits seamlessly within the project parameters. Custom dimensions reduce waste and often lead to cost savings, enhancing the project's efficiency and sustainability.
weld mesh size chart
Experience in selecting the right weld mesh size is invaluable, particularly in industries demanding high quality and reliability. Seasoned professionals understand the importance of consulting comprehensive size charts and collaborating with reputable suppliers who prioritize quality assurance. Verified supplier certifications and industry compliance standards should be non-negotiable criteria, providing peace of mind regarding the authenticity and durability of the mesh.
For those new to selecting weld mesh, expertise can be gained by consulting industry experts, exploring case studies, and engaging in hands-on training. Understanding the theoretical nuances combined with practical application enriches one's ability to make informed decisions in mesh selection, ultimately ensuring the project's success.
Trustworthiness in the supplier-provided information is crucial. Not all data available online or in printed size charts is equal; discrepancies in measurements or terminology can lead to costly mistakes. Verifying the integrity of this information through trusted industry publications or direct consultation with the manufacturers helps mitigate such risks.
In conclusion, navigating weld mesh size charts with proficiency involves a delicate balance of understanding material properties, application requirements, and supplier reliability. Professionals who cultivate expertise in this domain leverage their knowledge to enhance project outcomes, ensuring that they not only meet but exceed, the requisite industry standards. Through continuous learning and strategic supplier partnerships, the choice of weld mesh becomes a powerful asset, driving efficiency and innovation in diverse applications.