Wire mesh factories serve as pivotal players in various industries, from construction and agriculture to automotive and filtration. The burgeoning demand for versatile and resilient materials in these sectors underscores the significance of wire mesh production facilities. Delving into the intricate operations of a wire mesh factory, one discovers the confluence of cutting-edge technology, expert craftsmanship, and rigorous quality assurance—all contributing to the superior quality of the products manufactured.
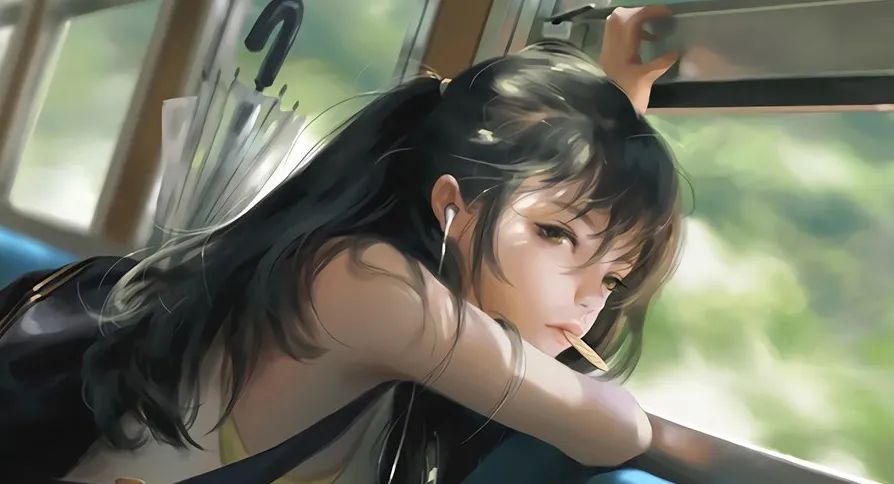
At the heart of every wire mesh factory lies the expertise of its workforce. The production process begins with selecting the finest quality raw materials, often high-grade steel or stainless steel, which are crucial for ensuring the durability and strength of the final product. Skilled technicians oversee the wire drawing process, transforming raw steel into fine, uniform wires through a series of precise operations. This stage requires meticulous attention to detail and profound knowledge of material properties to optimize tensile strength and flexibility.
Following wire drawing, the next phase is weaving or welding, whereby individual wires are intricately woven or welded to form mesh sheets of varying densities and designs. Each pattern, from plain to twill or Dutch weave, serves specific functions, catering to diverse industrial needs. For instance, tightly woven meshes are essential in filtration systems, whereas more open patterns find extensive use in reinforcement and fencing applications. The expertise of factory engineers and craftsmen is evident in their ability to tailor these patterns to exacting specifications, ensuring that each batch meets stringent industry standards.
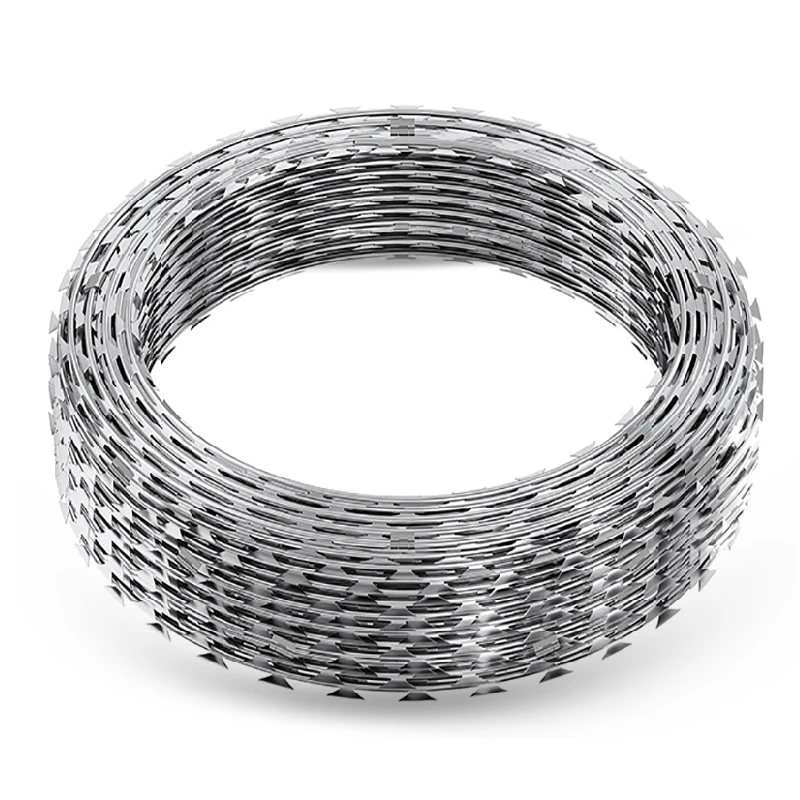
A significant factor distinguishing reputable wire mesh factories is their commitment to Authoritativeness and Trustworthiness within the industry. This is achieved through adherence to international quality standards such as ISO certifications, which guarantee that each product is manufactured under strict quality control measures. Rigorous testing protocols are implemented at various stages of production—tensile strength, corrosion resistance, and dimensional accuracy tests are conducted to ascertain product reliability and performance under demanding conditions.
wire mesh factory
Furthermore,
the application of advanced manufacturing technologies elevates the production capabilities of wire mesh factories. Automation plays a crucial role, enhancing precision and efficiency while minimizing human error. State-of-the-art machinery equipped with computer-aided design (CAD) systems allows for the customization of wire mesh products to meet unique customer specifications. Such technological integration not only boosts productivity but also positions the factory as a leader in innovation and adaptability within the marketplace.
In addition to technical prowess, the trustworthiness of a wire mesh factory is reinforced through transparent customer relations and sustainable practices. By offering comprehensive support, from product selection to post-sale services, these factories foster long-term partnerships with clients. Sustainability is a growing concern, and many factories are adopting eco-friendly practices such as recycling waste materials and utilizing energy-efficient machinery, which bolsters their reputation in a conscientious market.
In essence, a thriving wire mesh factory is a testament to the harmonious blend of experience, expertise, authority, and trustworthiness. By prioritizing quality, innovation, and customer satisfaction, these manufacturing powerhouses not only meet the diverse demands of global industries but also set benchmarks for excellence in wire mesh production. As industries continue to evolve, the role of wire mesh factories in fueling innovation and expansion becomes ever more crucial, ensuring that they remain indispensable assets to modern infrastructure and industrial applications.