Wire mesh welding is a revolutionary solution that has significantly improved the safety standards and efficiency in various industries. Understanding how this process works and why it's becoming the go-to option for many professionals is crucial for anyone looking to enhance project outcomes.
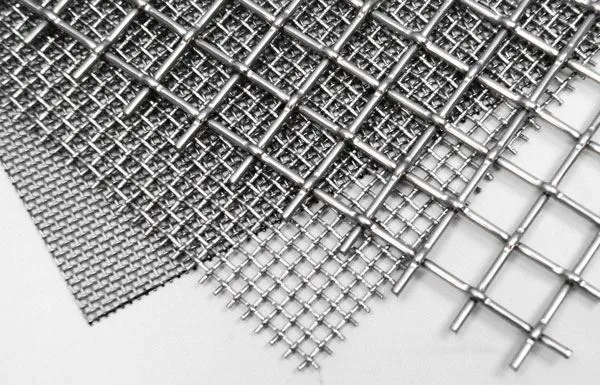
Wire mesh welding involves the automated welding of intersecting wires to form a robust grid or mesh made from steel or other durable metal materials. This grid can then be used in a range of applications, from construction reinforcement to industrial product assembly. What makes wire mesh welding a standout process is its blend of precision, speed, and strength—attributes essential for industries striving for high-quality standards.
From an experiential perspective, companies that have transitioned to using welded wire mesh report notable improvements in logistical efficiency. Unlike manually tied alternatives,
welded wire meshes are more uniform, leading to less waste and more reliable setup times. This uniformity is not merely about aesthetics; it significantly enhances the tensile strength of the mesh, making it a preferred choice in construction projects where safety is paramount. It creates less room for error in critical infrastructures, like bridges and commercial buildings, where precision engineering is critical.
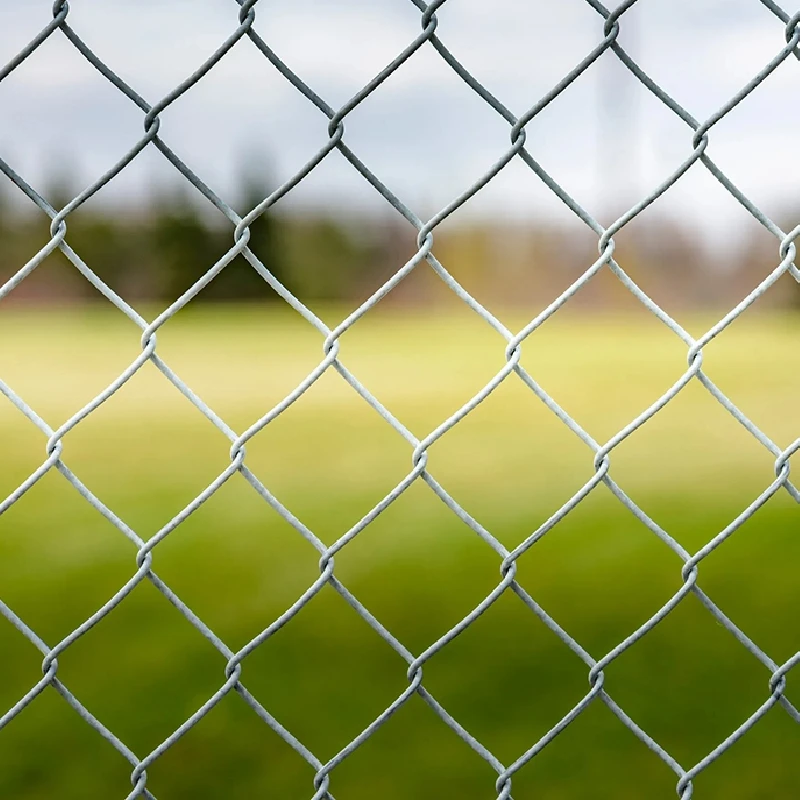
The expertise in wire mesh welding technology is reflected in the precise machinery used, such as CNC welders specifically designed for this task. Professionals operating these machines bring a wealth of knowledge, ensuring that each mesh is consistently manufactured to meet stringent industry standards. This level of expertise translates into more durable products that extend the lifespan of the structures they reinforce.
wire mesh welding
Moreover, the authoritative position of wire mesh welding in the industry can be attributed to its widespread adoption across various sectors. Leading construction firms and manufacturing giants have endorsed this technology, frequently citing its superiority over traditional methods. These endorsements are buttressed by comprehensive studies showcasing the enhanced load-bearing capacities of welded mesh versus non-welded alternatives. Such studies provide compelling evidence, solidifying welded mesh as not just an option but often a necessity for high-stakes projects.
Trustworthiness in wire mesh welding arises from rigorous testing and quality assurance measures that are adopted globally. Each welded section undergoes thorough checks to ensure no weak points exist—a crucial factor in upholding the safety measures of the entire structure it supports. Certifications from recognized institutions further validate the reliability of welded meshes. For instance, obtaining a Standard Wire Gauge (SWG) certification can provide additional assurance that the wire mesh meets specific gauge tolerance requirements, reflecting its top-notch quality.
One of the lesser-discussed yet highly significant benefits of wire mesh welding is its contribution to sustainability. The process minimizes waste during production and installation, and because welded meshes last longer, they reduce the frequency of replacements and repairs, leading to lower consumption of raw materials over time. This aspect aligns well with the growing demand for green construction methods and sustainable practices in the industry.
In conclusion, wire mesh welding is a multifaceted solution that surpasses traditional methods in safety, strength, efficiency, and sustainability. Its widespread industry acceptance underscores its credibility and expert endorsement, positioning it as the future of construction and manufacturing reinforcement technologies. For professionals planning their next project, adopting wire mesh welding might just be the transformative decision needed to elevate their project’s success.