Navigating the intricacies of weld mesh pricing requires a comprehensive understanding of various influencing factors, which only seasoned experts in the construction and manufacturing industries might possess. Weld mesh is indispensable in numerous applications, from construction sites to domestic gardens, and understanding its pricing helps businesses make informed purchasing decisions.
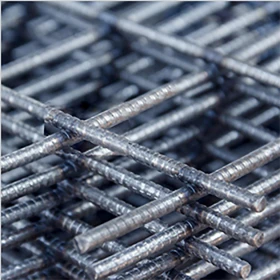
Primarily, the material composition significantly affects the weld mesh price. Mild steel and stainless steel are commonly used materials, with stainless steel generally being more expensive due to its anti-corrosive properties and longevity. Professionals in industries where exposure to harsh environmental conditions is a concern often prefer stainless steel, despite the higher cost, because it offers long-term savings on repairs and replacements.
The gauge of the wire and the size of the mesh also influence the price. A thicker gauge wire typically offers more strength and durability, which is crucial for specific engineering projects that demand structural integrity. Therefore, projects that cannot compromise on quality may require a larger initial investment in thicker gauge weld mesh. Meanwhile, the size of the mesh openings can dictate the amount of material used in production; smaller openings need more wire and manufacturing resources, thereby increasing costs.
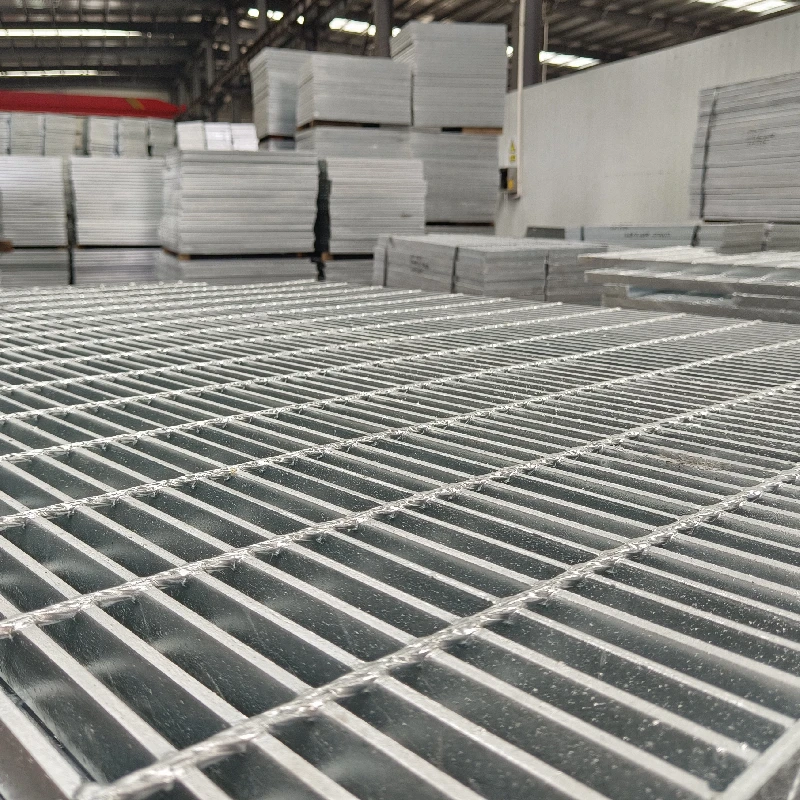
Manufacturing processes contribute to the price variations as well. Automated production lines with advanced welding technology might lower costs due to efficiencies gained in mass production, though the capital investment for such equipment is substantial. Companies at the forefront of welding technology, therefore, tend to provide competitive pricing while ensuring high-quality products.
Location plays a critical role too. Proximity to manufacturing plants can reduce transportation costs, impacting the overall price presented to consumers. In contrast, import duties and tariffs can significantly increase costs in regions far from production facilities. Consequently, sourcing local weld mesh suppliers might be economically advantageous, especially for large-volume orders.
weld mesh price
An often-overlooked factor is market demand. Construction booms and high industrial demands can lead to an increase in weld mesh prices due to supply constraints. Industry experts monitor global market trends to predict pricing shifts influenced by economic cycles.
These factors demonstrate the importance of expertise in choosing the right weld mesh product. Quotes from reputable suppliers should be thoroughly assessed. Ensuring that suppliers comply with international quality standards, such as ISO 9001, is crucial to mitigating risks associated with substandard materials. Newbies might not realize but engaging in long-term partnerships with suppliers can also provide cost benefits through negotiated deals and consistent quality assurance.
In reviewing weld mesh prices, it is crucial to balance cost with the value provided by the product's specifications and reliability, which directly correlate with project success. Detailed discussions with suppliers, coupled with site visits when possible, increasingly become critical practices among industry professionals to ensure investments in weld mesh do not compromise project integrity.
Ultimately, businesses looking to procure weld mesh can make wiser decisions by prioritizing experienced suppliers who offer certified products tailored to their needs. Trust in a supplier should be built on a foundation of past performance and industry reputation, assuring that the weld mesh adopted is not only cost-effective but also robust enough to meet specific project demands.