When considering concrete flooring, the reinforcement plays an essential role in preventing cracks and increasing the structural integrity of the project. Among various reinforcement options, wire mesh stands out as an effective, versatile, and widely-used solution. This article delves into the advantages, application techniques, and expertise required for incorporating wire mesh into concrete floors, all while showcasing its proven reliability in the construction industry.
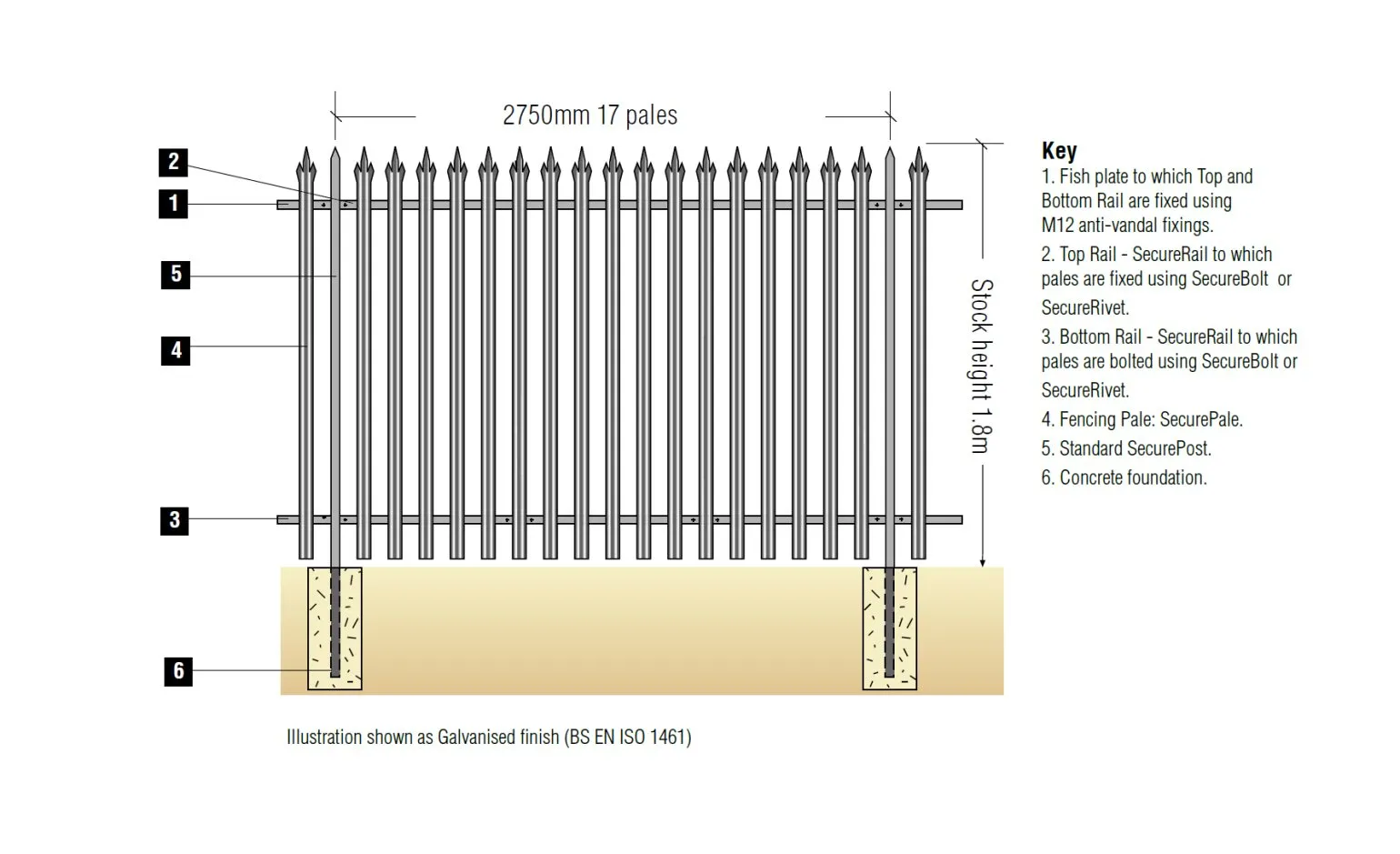
Wire mesh, often referred to as welded wire fabric or WWF, comprises a grid of steel wires spaced at regular intervals and welded at each intersection. This structure not only fortifies the concrete but also distributes loads more evenly, reducing stress concentrations that can lead to cracking. Construction professionals acknowledge the efficiency and durability provided by wire mesh, making it a staple in both residential and commercial concrete projects.
One primary advantage of using wire mesh in concrete floors is its ease of installation. Unlike rebar, which requires individual placement and tying, wire mesh can be laid in sheets or rolls over large areas quickly. This efficiency reduces labor costs and shortens project timelines, which is especially beneficial for large-scale projects where time and budget constraints are critical.
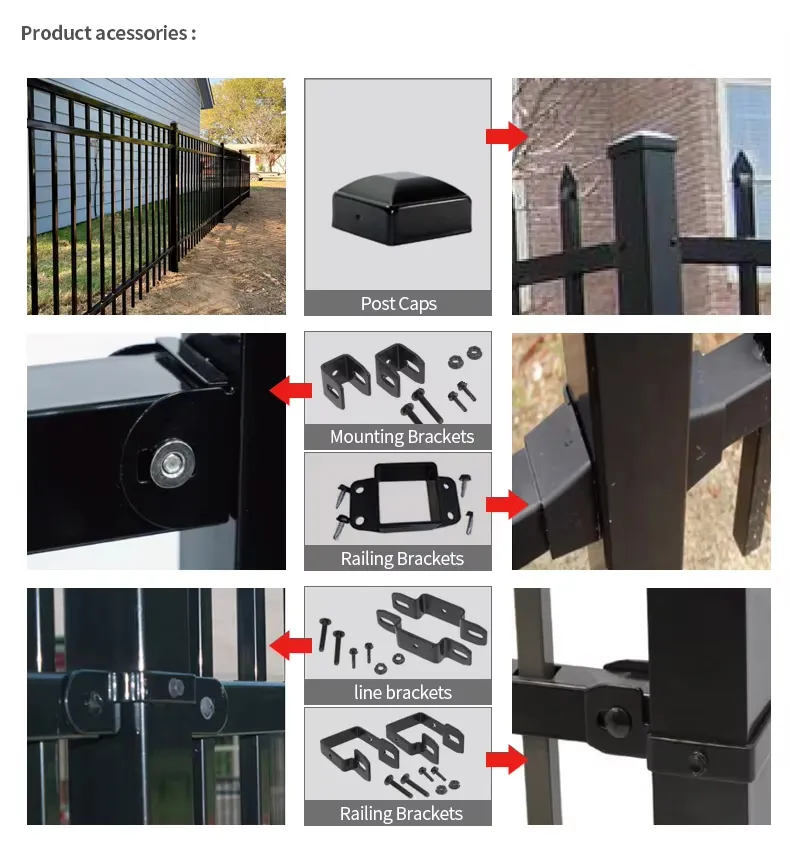
For those in the construction field, it's important to understand the specific requirements for each project. The gauge and spacing of the wire mesh depend on the load-bearing needs and environmental conditions of the site. Selecting the appropriate mesh involves consulting structural engineers who can provide insights based on soil analysis, expected usage loads, and regional climate variations. This expertise ensures that the concrete floor will perform optimally throughout its service life.
Experienced contractors also emphasize the importance of proper placement of wire mesh in the concrete slab. Ideally, the mesh should be positioned in the top third of the slab thickness, offering optimal tensile support where stresses are most significant. During the pour, spacers are often used to maintain this position, preventing the mesh from settling at the bottom where it loses its effectiveness.
wire mesh for concrete floor
Quality assurance doesn't end with installation. Monitoring the floor during the curing process is crucial to prevent common issues such as differential drying or shrinkage, which can still lead to cracking despite the reinforcement. Techniques such as wet curing or using curing compounds can mitigate these risks, further enhancing the durability of the floor.
Contractors adhering to industry best practices understand the long-term benefits of quality materials and craftsmanship. Wire mesh, when correctly implemented, offers concrete floors superior resilience against cracks due to thermal expansion, contraction, or heavy loads. This reliability has been documented in countless projects, from residential garages to commercial warehouses, underscoring its authority as a trusted reinforcing material.
The trustworthiness of wire mesh in concrete flooring applications is further reinforced by adherence to standards set by organizations such as the American Concrete Institute (ACI) and the National Ready Mixed Concrete Association (NRMCA). These bodies provide guidelines that ensure installations meet safety and performance criteria, assuring clients of the stability and longevity of their investment.
Overall, the integration of wire mesh in concrete floors is a testament to human ingenuity in civil engineering, marrying simplicity with efficiency to achieve robust structural integrity. As professionals continue to refine techniques and materials, wire mesh remains a cornerstone of modern construction, representing not only a technical choice but a strategic one for those seeking to optimize the balance between cost, performance, and durability.